The Engine harmonic balancer plays a crucial role in maintaining engine stability by reducing vibrations and ensuring smooth operation. Proper installation is key, and adhering to the 6.0 LS harmonic balancer torque specs is essential for optimal performance. This blog will delve into the significance of torque specifications, guiding readers on correct installation methods and best practices to enhance their vehicle’s longevity and efficiency.
Importance of Proper Torque Specs
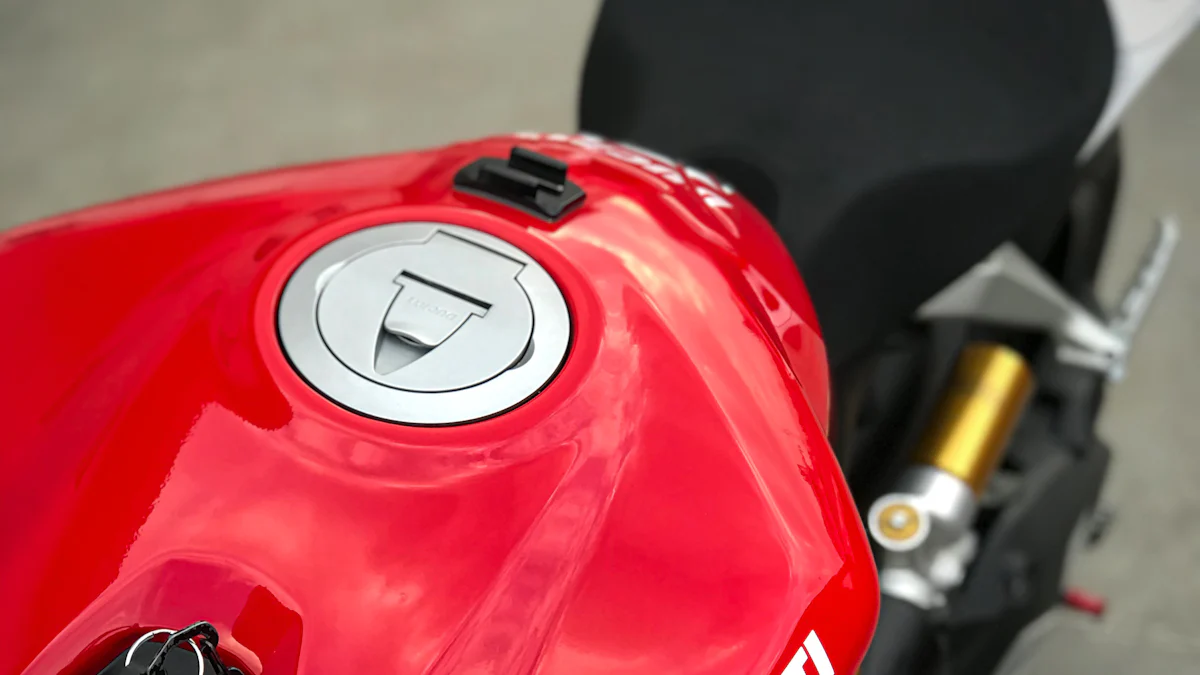
When it comes to the 6.0 LS harmonic balancer torque specs, precision is paramount for optimal engine performance. Understanding the significance of torque specifications is crucial in ensuring the harmonious operation of your vehicle’s engine system.
Understanding Torque Specifications
Definition and Importance
Torque specifications refer to the specific measurements detailing how tight a bolt or fastener should be when securing components together. In the context of harmonic balancers, these specifications dictate the exact force required to maintain stability and reduce vibrations within the engine. By adhering to these values, you guarantee that all parts are securely fastened, minimizing the risk of malfunctions or damage.
Impact on Engine Performance
The impact of correct torque specifications on engine performance cannot be overstated. When each component, including the harmonic balancer, is tightened to the manufacturer’s recommended settings, it ensures that the engine operates smoothly and efficiently. Deviating from these specifications can lead to imbalances, increased vibrations, and potential long-term damage to critical engine parts.
6.0 LS Harmonic Balancer Torque Specs
Standard Torque Values
For a 6.0 LS engine, standard torque values for the harmonic balancer typically revolve around 240 ft-lbs. This specific measurement is carefully calculated to provide optimal stability and reduce torsional vibrations in the crankshaft, promoting overall engine longevity and performance.
Alternative Torque Methods
In addition to traditional torque values, alternative methods exist for torquing the harmonic balancer effectively. One such method involves initially tightening the bolt to 37 ft-lb and then rotating it an additional 140 degrees. This approach ensures a secure fit while also distributing force evenly across all components.
Staging Lane Thread Starter
Community Insights
Engaging with automotive communities can offer valuable insights into best practices for torquing harmonic balancers. Enthusiasts and professionals alike often share their experiences and recommendations, shedding light on effective techniques and common pitfalls to avoid during installation.
Common Mistakes to Avoid
Despite its importance, torquing the harmonic balancer can sometimes lead to errors if not done correctly. Common mistakes include overtightening or undertightening bolts, neglecting proper alignment procedures, or using incorrect tools for installation. By being aware of these pitfalls, individuals can ensure a smooth and successful torquing process.
Torque Specifications and Methods
Standard Torque Procedure
When it comes to the 6.0 LS engines, adhering to proper torque specifications and sequence is crucial for maintaining the integrity of the vehicle’s components. This process ensures that fasteners are tightened in the correct order and with the appropriate amount of force, preventing potential issues down the line.
Step-by-Step Guide
- Begin by identifying the specific torque requirements outlined in the service information for your vehicle. These specifications are essential for each component’s stability and overall performance.
- Use a calibrated torque wrench to apply the necessary force accurately. This tool allows you to tighten fasteners to the manufacturer’s recommended settings with precision.
- Follow a systematic approach when torquing components, starting from critical areas such as the crankshaft balancer bolt. Ensuring that each fastener is secured properly is key to preventing any future complications.
- Verify each fastener after torquing to confirm that it meets the specified requirements. This step guarantees that all components are securely in place, ready for optimal functionality.
Required Tools
- Calibrated Torque Wrench: An essential tool for achieving accurate torque values on critical fasteners.
- Service Information Manual: Provides detailed instructions on torque specifications for various components in your vehicle.
- Safety Gear: Ensure you have appropriate safety equipment such as gloves and goggles to protect yourself during maintenance tasks.
- Fastening Hardware: Quality bolts and nuts compatible with your vehicle’s specifications are necessary for secure installations.
Alternative Torque Methods
In addition to following standard torque procedures, alternative methods can offer effective ways of securing components like the crankshaft balancer bolt.
37 ft-lb Plus 140 Degrees
One alternative method involves an initial tightening of 37 ft-lb followed by rotating the bolt an additional 140 degrees. This technique provides a secure fit while distributing force evenly across critical areas, enhancing overall stability.
Using Old Bolt for Initial Tightening
Another practice commonly observed is using the old bolt for initial tightening before replacing it with a new one. While this method may seem unconventional, it can help establish an initial hold before transitioning to a new, reliable fastener for long-term use.
Importance of Following GM Manual
The GM manual serves as a comprehensive guide detailing manufacturer recommendations and best practices for maintaining your vehicle’s performance through proper torquing procedures.
Manufacturer Recommendations
GM specifies precise torque values and sequences for nearly every fastener within their vehicles. By adhering to these recommendations, you ensure that each component operates optimally without risking damage or malfunctions.
Risks of Deviating from Specs
Deviation from manufacturer-recommended torque specifications poses significant risks to your vehicle’s functionality and safety. Incorrectly torqued components can lead to imbalances, increased vibrations, and potential failures that compromise overall performance.
By following GM manual guidelines diligently, you prioritize safety, reliability, and longevity in your vehicle’s operation while minimizing unforeseen complications arising from improper torquing practices on critical components like harmonic balancers and crankshaft bolts.
Best Practices for Installation
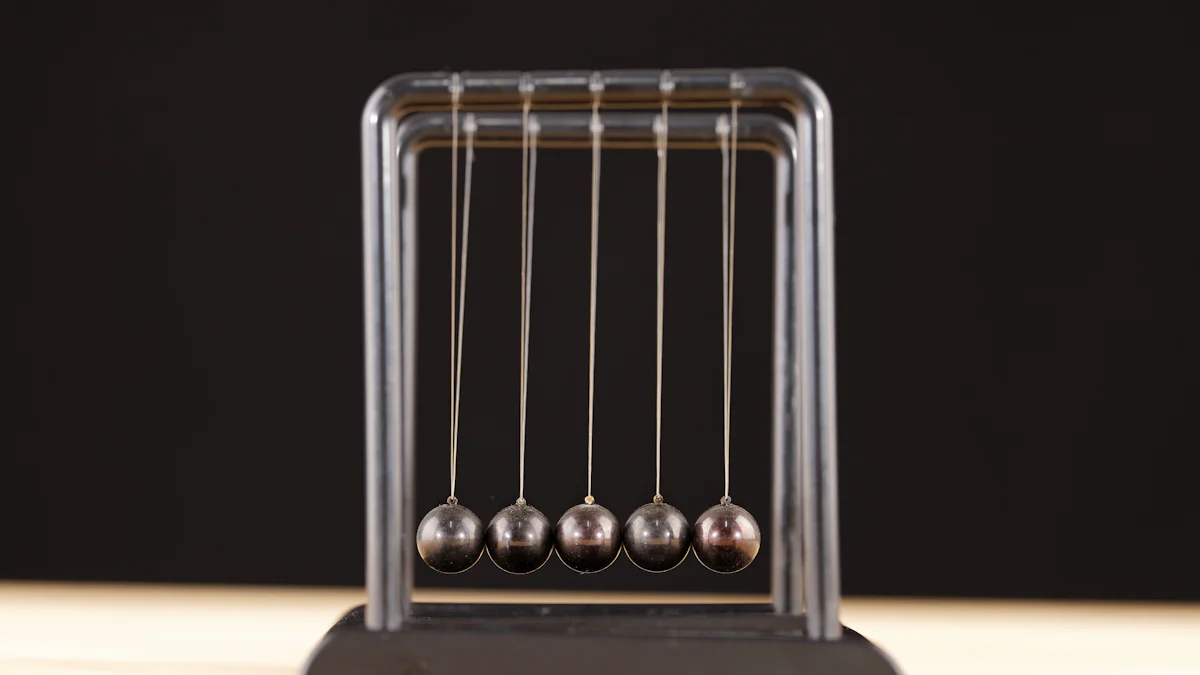
Preparing for Installation
When installing a harmonic balancer, meticulous preparations are essential to ensure a smooth and successful process. By following these necessary steps, individuals can set the stage for a seamless installation without compromising on quality or safety.
Necessary Preparations
- Gather all tools required for the installation, including a calibrated torque wrench, safety gear such as gloves and goggles, and high-quality fastening hardware.
- Inspect the harmonic balancer and surrounding components for any signs of damage or wear that may affect the installation process.
- Clean the mounting surface thoroughly to remove any debris or contaminants that could hinder proper alignment during installation.
- Ensure that the vehicle is securely positioned on stable ground with ample space to maneuver around the engine bay effectively.
Safety Precautions
- Prioritize personal safety by wearing appropriate protective gear throughout the installation process to prevent injuries from sharp edges or moving parts.
- Disconnect the vehicle’s battery to eliminate any risk of electrical shock while working near sensitive components.
- Use caution when handling heavy components like the harmonic balancer to avoid strain or injury, employing proper lifting techniques when necessary.
- Double-check all connections and fasteners post-installation to confirm that everything is securely in place before starting the engine.
Installation Process
The installation process of a harmonic balancer demands precision and attention to detail to guarantee optimal performance and longevity for your vehicle’s engine system. By following these step-by-step instructions diligently, enthusiasts can navigate through the installation seamlessly.
Step-by-Step Instructions
- Begin by aligning the keyway on the crankshaft with the corresponding slot on the harmonic balancer, ensuring a perfect fit before proceeding.
- Gently slide the harmonic balancer onto the crankshaft, taking care not to force it into place but allowing it to seat naturally against the mounting surface.
- Thread the new bolt into position by hand initially, ensuring that it engages smoothly with no resistance before using a torque wrench for final tightening.
- Gradually tighten the bolt in a star pattern sequence, alternating between bolts to distribute force evenly across all points of contact until reaching the specified torque value.
Ensuring Proper Alignment
- Verify that the harmonic balancer sits flush against the crankshaft hub without any gaps or misalignments that could lead to vibrations or instability during operation.
- Check for uniform spacing between the harmonic balancer and surrounding components to guarantee adequate clearance for rotational movement without interference.
- Confirm that all fasteners are tightened securely according to manufacturer specifications, preventing any potential issues arising from loose connections post-installation.
Post-Installation Checks
After completing harmonic balancer install, thorough post-installation checks are crucial in confirming that everything is in order and ready for optimal engine performance.
Verifying Torque
- Utilize a calibrated torque wrench to recheck all fasteners’ torque values, ensuring they meet or exceed manufacturer recommendations for secure installations.
- Perform a visual inspection of each connection point to identify any signs of loosening or misalignment that may require immediate attention before further operation.
Inspecting for Issues
- Conduct a test run of your vehicle post-installation, paying close attention to any unusual noises, vibrations, or performance issues that may indicate improper installation of the harmonic balancer.
- Monitor engine operation closely over time, noting any changes in performance or stability that could be attributed to faulty installation practices requiring correction.
In the realm of automotive maintenance, precision reigns supreme when it comes to torque specs for critical components like the harmonic balancer. By adhering to the recommended specifications, individuals safeguard their vehicles against potential malfunctions and ensure optimal engine performance. The significance of using a calibrated torque wrench cannot be overstated, especially for fasteners like head bolts and lug nuts/studs. While time constraints may tempt shortcuts, investing in proper torquing practices ultimately pays dividends in safety and longevity. Remember, in the world of mechanics, accuracy trumps haste.
Post time: May-31-2024