Automotive exhaust manifolds play a vital role in collecting and expelling exhaust gases from the engine after combustion. The choice of material for Performance exhaust manifold is crucial, impacting its reliability and durability. As the market trends show a shift towards lightweight alloys, the demand for efficient exhaust systems is on the rise. In this blog, we delve into the possibilities of enhancing exhaust manifold longevity through coatings like powder coating and ceramic coating. Can you powder coat exhaust manifolds? Let’s explore how these protective layers can safeguard manifolds from heat damage and corrosion while improving overall performance.
Analysis of Exhaust Manifold
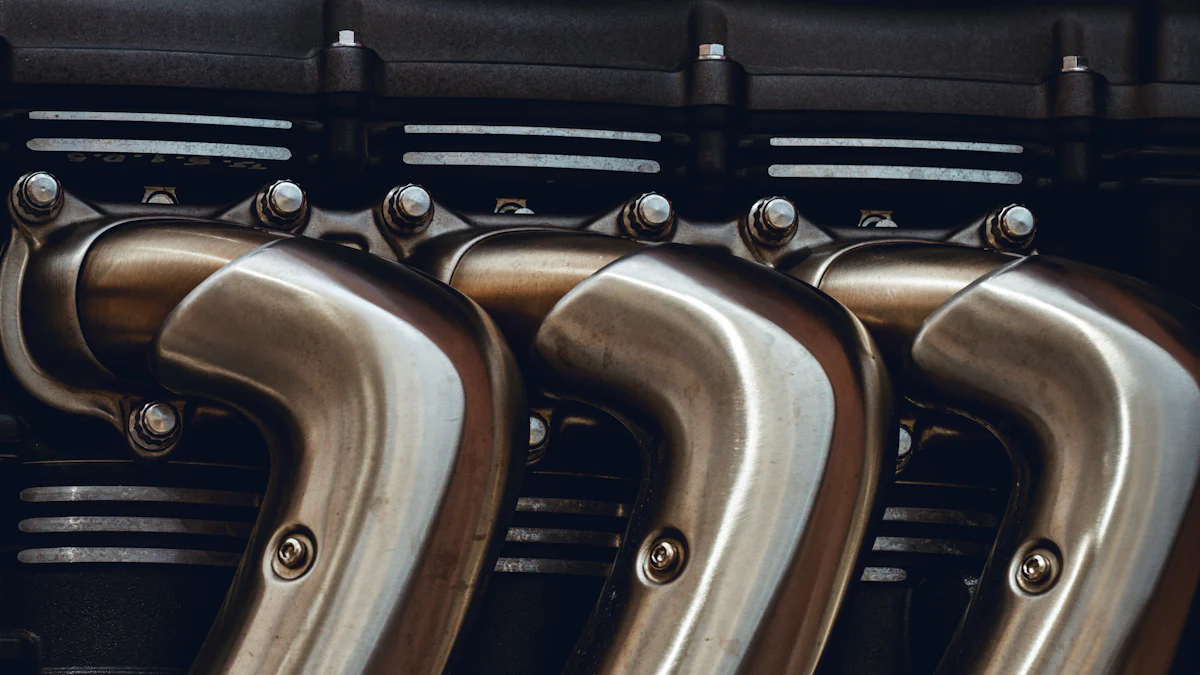
Exhaust manifold plays a critical role in the efficient operation of an engine by collecting and expelling exhaust gases. Understanding the properties of exhaust manifolds is essential to grasp their significance in engine systems.
Properties of Exhaust Manifolds
Material Composition
The material composition of exhaust manifolds significantly impacts their performance and longevity. Increasing use of lightweight and advanced alloys has become a key trend driving market growth. Automobile manufacturers have shifted towards tubular steel exhaust pipes on low-end vehicles to enhance overall system performance. The choice of material is crucial as it directly influences the reliability and durability of exhaust manifolds.
Function in Engine Systems
The functionality of exhaust manifolds is fundamental in ensuring optimal engine performance. These components are responsible for gathering exhaust fumes post-combustion, directing them towards the catalytic converter for emission control. Therefore, selecting the right material for manufacturing exhaust manifolds is paramount to maintaining engine efficiency and reducing harmful emissions.
Common Issues with Exhaust Manifolds
Heat Damage
Exhaust manifold suffers from high temperatures generated during engine operation, making them susceptible to heat damage over time. The intense heat exposure can lead to thermal degradation, warping, or even cracking of the manifold structure. Proper coatings like ceramic coatings can provide thermal insulation, enhancing heat resistance and prolonging manifold lifespan.
Corrosion
Another common issue that exhaust manifolds face is corrosion due to exposure to harsh environmental conditions and corrosive elements present in exhaust gases. Corrosion weakens the structural integrity of the manifold, potentially leading to leaks or failures. Implementing protective coatings such as zirconia powder can effectively combat corrosion, preserving the manifold’s functionality and longevity.
Exhaust
Exhaust systems are integral components of an engine, responsible for managing heat and controlling emissions effectively. Understanding the role of exhaust in engine performance sheds light on its critical functions.
Role of Exhaust in Engine Performance
Heat Management
Effective heat management is crucial for engine performance optimization. By efficiently dissipating heat generated during combustion, exhaust systems prevent overheating and maintain operational efficiency. The use of advanced alloys like tubular steel exhaust pipes enhances heat management capabilities, contributing to improved overall engine performance.
Emission Control
Emission control is a key aspect of exhaust systems, ensuring the reduction of waste toxic gases released during engine operation. Through proper filtration and treatment mechanisms, exhaust systems play a vital role in minimizing environmental impact and promoting cleaner air quality.
Impact of Coatings on Exhaust Systems
Powder Coating
The application of powder coating on exhaust components has gained attention for its protective properties. While powder coating offers aesthetic appeal and corrosion resistance in various applications, its suitability for high-temperature environments like exhaust manifolds remains a topic of debate due to durability concerns.
Ceramic Coating
Ceramic coatings, on the other hand, have demonstrated superior thermal resistance and durability in demanding conditions. With the ability to withstand extreme temperatures and provide effective heat insulation, ceramic coatings offer a reliable solution for enhancing the longevity and performance of exhaust manifolds.
Exhaust Manifold with Ceramic
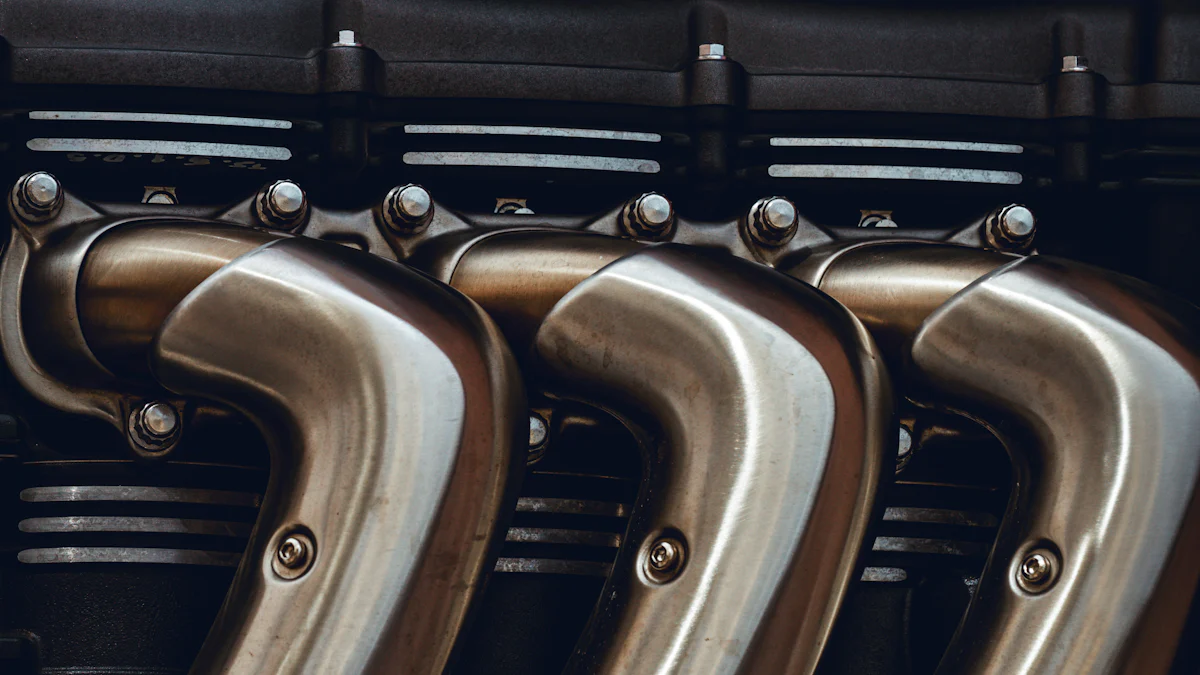
Benefits of Ceramic Coating
Ceramic coatings offer exceptional heat resistance and durability for exhaust manifolds, ensuring optimal performance and longevity. The application of ceramic coatings on exhaust components has been a game-changer in the automotive industry, providing superior protection against extreme temperatures and corrosive environments.
- Heat Resistance: Ceramic-coated exhaust manifolds exhibit remarkable heat resistance properties, allowing them to withstand the intense temperatures generated during engine operation. This heat tolerance is essential for preventing thermal degradation and structural damage, ensuring the manifold’s functionality under high-stress conditions.
- Durability: The durability of ceramic coatings significantly enhances the lifespan of exhaust manifolds by providing a robust protective layer. By forming a strong bond with the manifold surface, ceramic coatings effectively shield it from heat-induced wear and corrosion, contributing to long-term reliability and performance.
Case Studies and Experimental Results
Exploring TiO2 and ZrO Coatings through case studies and experimental analyses sheds light on the effectiveness of ceramic-coated exhaust manifolds in real-world applications. These studies provide valuable insights into the performance enhancements achieved through ceramic coatings compared to uncoated manifolds.
Case Study: Application of TiO2 Coating
- The application of TiO2 coating on exhaust manifolds demonstrated a significant improvement in heat insulation properties.
- The coated manifold exhibited enhanced thermal stability, reducing the risk of heat-related damage and improving overall efficiency.
- Comparative analysis revealed that TiO2-coated manifolds outperformed their uncoated counterparts in terms of temperature management and longevity.
Experimental Results: ZrO Coatings
- Experimental data on ZrO coatings showcased superior corrosion resistance capabilities when applied to exhaust manifolds.
- The ZrO-coated manifolds exhibited enhanced durability against corrosive elements present in exhaust gases, prolonging their operational lifespan.
- Comparative analysis highlighted the effectiveness of ZrO coatings in mitigating corrosion-induced degradation compared to uncoated manifolds.
By leveraging advanced ceramic coating technologies such as TiO2 and ZrO, manufacturers can enhance the performance and durability of exhaust systems while ensuring optimal engine efficiency.
Manifold Protects Super Boat
Importance of Coatings in Marine Applications
In marine applications, coatings play a crucial role in safeguarding vessels from the harsh conditions of the sea. The heat dissipation and corrosion resistance properties of coatings are particularly vital for maintaining the structural integrity and longevity of marine components.
- Heat Dissipation: Proper coatings on marine vessels facilitate efficient heat dissipation, preventing overheating and ensuring optimal performance under extreme conditions. The ability of coatings to dissipate heat effectively contributes to the overall functionality and durability of marine equipment.
- Corrosion Resistance: Coatings provide a protective barrier against corrosion, which is a common challenge faced by marine vessels due to constant exposure to saltwater and environmental elements. By enhancing corrosion resistance, coatings help prolong the lifespan of marine components and reduce maintenance costs.
Case Study: Cutting-Edge Super Boat
The application of advanced coatings on the cutting-edge Super Boat has led to significant improvements in performance and longevity, setting new standards in marine engineering.
- Performance Improvements: Through the implementation of innovative coatings, the Super Boat has experienced remarkable enhancements in speed, fuel efficiency, and overall operational capabilities. The optimized performance achieved through coating technologies has elevated the Super Boat’s competitiveness in maritime competitions.
- Longevity: The durability and resilience provided by specialized coatings have extended the operational lifespan of the Super Boat, reducing wear and tear caused by prolonged exposure to marine environments. By protecting critical components from corrosion and heat damage, coatings have ensured sustained performance and reliability over time.
Sponsored Content
- The collaboration between leading coating manufacturers and maritime engineers has revolutionized the protection of marine vessel hulls through advanced coating solutions.
- Sponsored research initiatives have demonstrated the effectiveness of tailored coatings in enhancing vessel durability, safety, and efficiency in challenging maritime conditions.
By prioritizing the application of high-quality coatings on marine vessels like the Super Boat, industry professionals can achieve superior performance outcomes while preserving the structural integrity and longevity of critical components.
Reduction of Heat Dissipation
Understanding the mechanisms of heat dissipation is crucial for optimizing engine performance and ensuring the longevity of critical components. Coatings play a pivotal role in managing heat effectively, thereby enhancing overall operational efficiency.
Role of Coatings
Coatings act as a protective barrier against excessive heat buildup, preventing thermal stress on engine parts. By applying specialized coatings to exhaust manifolds and other high-temperature components, manufacturers can mitigate heat-related issues and improve system reliability.
Experimental Data
Scientific research findings highlight the significance of heat dissipation coatings in various industries. Studies reveal that tailored solutions based on specific application areas offer effective thermal management solutions, contributing to enhanced performance and durability.
Benefits of Reduced Heat Dissipation
Optimizing heat dissipation offers substantial benefits for engine operation and component lifespan. By efficiently managing heat through advanced coatings, manufacturers can achieve:
- Improved Engine Efficiency: Enhanced heat dissipation leads to better temperature regulation within the engine, optimizing combustion processes and overall performance.
- Extended Component Longevity: Effective heat management prolongs the lifespan of critical engine parts by reducing thermal stress and minimizing wear over time.
Incorporating advanced coatings designed for optimal heat dissipation not only enhances system efficiency but also ensures long-term reliability in demanding operating conditions.
Can You Powder Coat Exhaust Manifolds?
Analysis of Powder Coating Suitability
When considering the application of powder coating on exhaust manifolds, assessing its temperature tolerance is paramount. Unlike ceramic coatings that offer exceptional heat resistance, powder coatings may not withstand the extreme temperatures experienced in exhaust systems. The durability concerns surrounding powder coatings raise questions about their long-term effectiveness in protecting exhaust manifolds.
Temperature Tolerance
- Powder Coating Limitations: While powder coatings provide a thick and tough finish, their temperature tolerance may not meet the demands of high-performance exhaust systems. The risk of melting off under intense heat poses a significant concern for the longevity of powder-coated exhaust manifolds.
- Ceramic Coating Superiority: In contrast, ceramic coatings like those offered by Jet-Hot are specifically designed for high-temperature applications. Custom ceramic coatings demonstrate durability and reliability, ensuring optimal protection for exhaust manifolds exposed to extreme heat levels.
- Comparative Insights: Cerakote High Temperature Ceramic Coatings stand out for simulating real-world exhaust conditions and undergoing rigorous testing processes. This unique capability sets ceramic coatings apart from traditional powder coatings in terms of performance and longevity.
Durability Concerns
- Longevity Considerations: When evaluating coating options for exhaust manifolds, durability plays a crucial role in determining the protective capabilities against heat and corrosion. At-home ceramic coatings, when applied with proper preparation techniques, can rival professional-grade solutions like those from Jet-Hot in terms of durability and effectiveness.
- Preventive Measures: Proper prep work before applying ceramic coatings enhances their adhesion and longevity on exhaust manifolds. By addressing surface preparation diligently, enthusiasts can achieve durable and reliable results comparable to professional-grade applications.
Exhaust Manifolds Reduce Engine
Impact on Engine Performance
Vibration Reduction
Exhaust manifolds and risers are crucial components in inboard engines, responsible for carrying hot exhaust gases away from the engine. These large metal castings play a significant role in reducing engine vibrations, ensuring smooth operation during combustion cycles. By efficiently channeling exhaust gases through the manifold and riser system, the engine experiences minimized vibrations, leading to enhanced performance and longevity.
Emission Control
Inboard engines equipped with exhaust manifolds benefit from effective emission control mechanisms. The separation of exhaust gases through individual manifolds allows for optimized emission treatment processes, reducing harmful pollutants released into the environment. By directing exhaust fumes towards the risers and subsequently out of the engine system, exhaust manifolds contribute to maintaining compliance with emission regulations and promoting cleaner air quality.
Future Developments
Emerging Technologies
The evolution of engine bay temperature management technologies continues to drive advancements in exhaust manifold design. Innovations focused on enhancing heat dissipation and optimizing airflow within the engine compartment are shaping the future of inboard engine systems. From advanced materials to integrated cooling solutions, emerging technologies aim to lower lower engine bay temperature, improve overall efficiency, and prolong component lifespan.
Industry Trends
The automotive industry is witnessing a shift towards more sustainable practices in exhaust manifold manufacturing. With a growing emphasis on eco-friendly solutions, manufacturers are exploring alternative materials and coatings that reduce environmental impact without compromising performance. Industry trends indicate a transition towards lightweight alloys, innovative heat-resistant ceramics, and efficient cooling strategies to meet stringent emissions standards while enhancing engine reliability.
Recapping the essential points discussed reveals the critical role of coatings in enhancing exhaust manifold durability. Ceramic coatings, especially custom options like those from Jet-Hot, offer superior protection against heat and corrosion. While at-home ceramic coatings can rival professional solutions with proper preparation, the choice between powder coating and ceramic coating is clear. Opting for a durable ceramic coating ensures long-term performance and reliability for exhaust manifolds, setting a new standard in protective solutions for high-performance engines.
Post time: Jun-13-2024