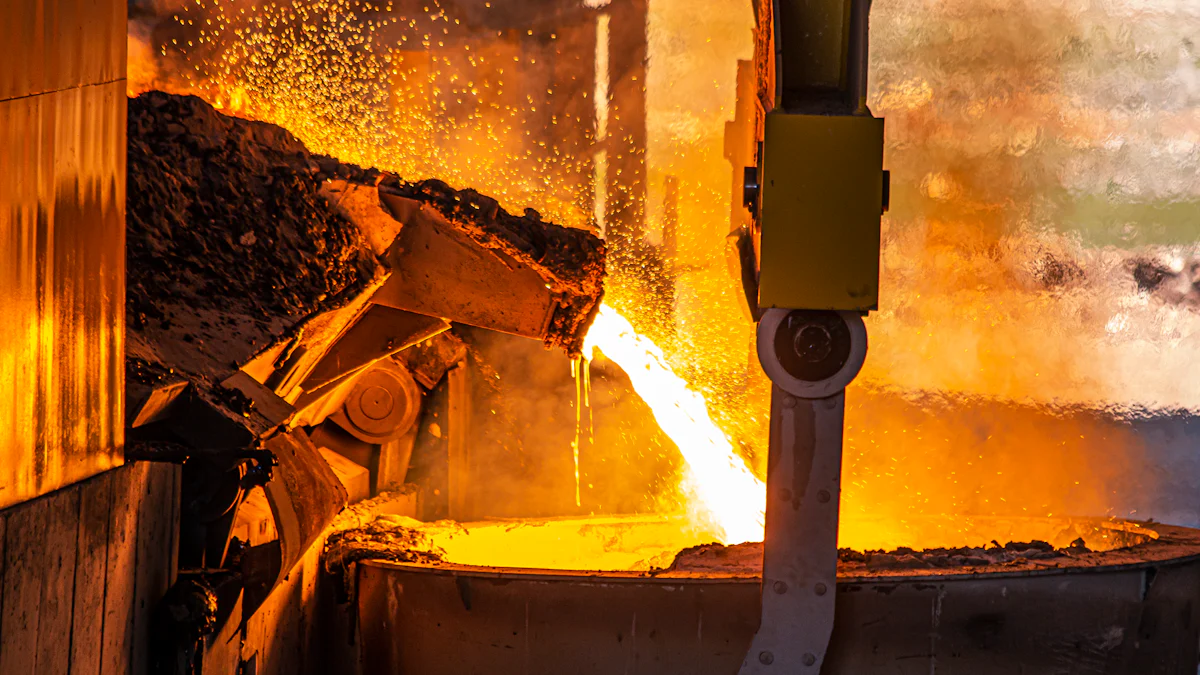
Manifolds play a crucial role in engine performance. These components channel exhaust gases away from the engine, impacting efficiency and power output. The choice of material for an exhaust manifold significantly influences its effectiveness. A cast iron exhaust manifold offers durability and heat retention, making it a popular choice. However, advancements in material technology have introduced alternatives like cast steel, which provide enhanced strength and corrosion resistance. Understanding these differences helps you make informed decisions that enhance vehicle performance.
Understanding Manifolds
What is a Manifold?
Definition and Function
A manifold serves as a critical component in an engine’s exhaust system. The manifold collects exhaust gases from multiple cylinders into one pipe. This process ensures efficient expulsion of gases from the engine. The design of the manifold impacts how effectively gases flow, which directly affects engine performance.
Types of Manifolds
Manifolds come in different types, each suited for specific applications. The two primary types include exhaust manifolds and intake manifolds. Exhaust manifolds channel gases away from the engine, while intake manifolds distribute air to the engine’s cylinders. Each type plays a distinct role in maintaining optimal engine function.
Importance in Engine Performance
Impact on Efficiency
Manifolds significantly influence engine efficiency. Properly designed manifolds enhance the flow of exhaust gases, reducing back pressure. This reduction leads to improved fuel efficiency and increased power output. A study highlighted that steel manifolds, especially stainless steel versions, can reduce heat loss, leading to increased horsepower and performance.
Role in Emission Control
Manifolds also play a vital role in emission control. By efficiently channeling exhaust gases, manifolds help maintain lower emissions. The design and material of the manifold impact how well it controls emissions. For instance, ceramic coatings on manifolds can decrease temperatures, which enhances the performance of aftertreatment systems. This enhancement contributes to cleaner emissions and better environmental compliance.
Material Properties
Cast Iron Exhaust Manifold
Composition and Characteristics
A cast iron exhaust manifold consists of iron mixed with carbon and silicon. This composition provides excellent heat retention and durability. The thick walls of cast iron help in insulating the manifold, which reduces under-hood temperatures. Cast iron conducts heat better than steel, which aids in maintaining a stable engine temperature.
Advantages and Disadvantages
Advantages of a cast iron exhaust manifold include its cost-effectiveness and longevity. Cast iron manifolds are less expensive to produce compared to other materials. The durability of cast iron ensures a long lifespan, making it a reliable choice for many vehicles. The material’s ability to withstand high temperatures without significant expansion helps maintain the integrity of the exhaust system.
Disadvantages involve performance limitations. Cast iron manifolds are heavier and can restrict exhaust flow, which may reduce engine power. Although ceramic coatings can enhance performance slightly, cast iron still produces less power than tubular steel headers. The thickness of cast iron also means more weight, which can affect overall vehicle performance.
Cast Steel
Composition and Characteristics
Cast steel manifolds consist of iron alloyed with carbon and other elements such as manganese. This composition results in a stronger and more corrosion-resistant material compared to cast iron. Cast steel manifolds are often used in high-performance applications due to their strength and ability to handle extreme conditions.
Advantages and Disadvantages
Advantages of cast steel include its superior strength and resistance to corrosion. The material’s ability to withstand thermal expansion and contraction makes it suitable for high-performance engines. Cast steel manifolds can reduce heat loss, which enhances horsepower and overall engine performance.
Disadvantages involve higher costs and potential issues with thermal expansion. Cast steel manifolds are generally more expensive than cast iron options. The material’s tendency to expand and contract during heat cycles can lead to problems with bolts or studs loosening over time. Despite these challenges, the performance benefits often outweigh the drawbacks for enthusiasts seeking maximum power output.
Performance Comparison
Durability and Longevity
Resistance to Wear and Tear
Cast iron exhaust manifolds offer excellent resistance to wear and tear. The material’s robust nature ensures a long lifespan, even under harsh conditions. Cast iron maintains structural integrity despite exposure to high temperatures and corrosive gases. This makes cast iron a reliable choice for many vehicles.
Cast steel manifolds, on the other hand, provide superior strength. The alloy composition enhances resistance to cracking and deformation. Cast steel withstands extreme conditions better than cast iron. This makes cast steel suitable for high-performance applications.
Maintenance Requirements
Maintenance requirements differ between the two materials. Cast iron manifolds require minimal upkeep. The thick walls and heat retention properties reduce the need for frequent inspections. Regular checks for rust or corrosion ensure optimal performance.
Cast steel manifolds demand more attention. The material’s tendency to expand and contract during heat cycles necessitates regular bolt and stud checks. Ensuring tight connections prevents potential leaks or failures. Proper maintenance extends the manifold’s lifespan and performance.
Thermal Conductivity
Heat Retention and Dissipation
Cast iron manifolds excel in heat retention. The material’s density allows it to absorb and retain heat effectively. This characteristic helps maintain a stable engine temperature. However, excessive heat retention may lead to increased under-hood temperatures.
Cast steel manifolds offer better heat dissipation. The alloy’s composition allows for quicker heat release. This reduces the risk of overheating and improves overall engine efficiency. Enhanced heat dissipation contributes to improved horsepower and performance.
Impact on Engine Temperature
Engine temperature management varies between the materials. Cast iron manifolds help stabilize engine temperatures. The material’s heat retention properties prevent rapid temperature fluctuations. This stability benefits engines operating under consistent loads.
Cast steel manifolds promote cooler engine operation. The material’s ability to dissipate heat quickly reduces the risk of overheating. Engines benefit from improved efficiency and performance. Cooler temperatures also enhance the longevity of engine components.
Cost and Availability
Price Comparison
Cast iron manifolds offer a cost-effective solution. The manufacturing process is less expensive compared to cast steel. This affordability makes cast iron a popular choice for budget-conscious consumers. The lower price point does not compromise durability or performance.
Cast steel manifolds come with a higher price tag. The superior strength and corrosion resistance justify the additional cost. Enthusiasts seeking maximum performance often choose cast steel despite the expense. The investment pays off in terms of enhanced engine output and reliability.
Market Availability
Market availability influences material choice. Cast iron manifolds are widely available. The material’s popularity ensures easy access for consumers. Replacement parts and aftermarket options abound.
Cast steel manifolds may have limited availability. The specialized nature of the material restricts options. High-performance applications often dictate the use of cast steel. Consumers may need to source parts from specific suppliers or manufacturers.
Application Suitability
Best Uses for Cast Iron Exhaust Manifolds
Ideal Scenarios
Cast iron exhaust manifolds suit vehicles requiring durability and heat retention. Heavy-duty trucks benefit from cast iron’s robust nature. The material withstands high temperatures without significant expansion. Vehicles operating in extreme conditions find cast iron advantageous. The thick walls of cast iron help reduce under-hood noise. This feature enhances the driving experience.
Limitations
Cast iron manifolds face limitations in performance applications. The weight of cast iron affects vehicle dynamics. Sports cars may experience reduced power output. The restrictive flow of exhaust gases limits engine efficiency. High-performance engines require better exhaust flow. Cast iron’s inability to expand can lead to cracking under extreme stress.
Best Uses for Cast Steel Manifolds
Ideal Scenarios
Cast steel manifolds excel in high-performance vehicles. Racing cars benefit from cast steel’s strength. The material handles extreme conditions effectively. Engines with high horsepower gain from cast steel’s thermal properties. The ability to dissipate heat quickly improves engine efficiency. Enthusiasts seeking maximum power choose cast steel.
Limitations
Cast steel manifolds come with higher costs. Budget-conscious consumers may find cast steel expensive. The material requires regular maintenance checks. Expansion during heat cycles necessitates bolt inspections. Availability of cast steel parts may be limited. Specific suppliers often provide cast steel manifolds.
The comparison between cast iron and cast steel manifolds highlights key differences in performance and application suitability. Cast iron offers durability and cost-effectiveness, making it ideal for heavy-duty vehicles. Cast steel provides superior strength and heat dissipation, enhancing high-performance engines. Understanding material behavior is crucial for designing efficient manifolds. Material selection impacts product longevity and performance. Choose cast iron for durability and affordability. Opt for cast steel for enhanced performance and strength. Consider specific needs and applications when selecting the right manifold material.
Post time: Sep-02-2024