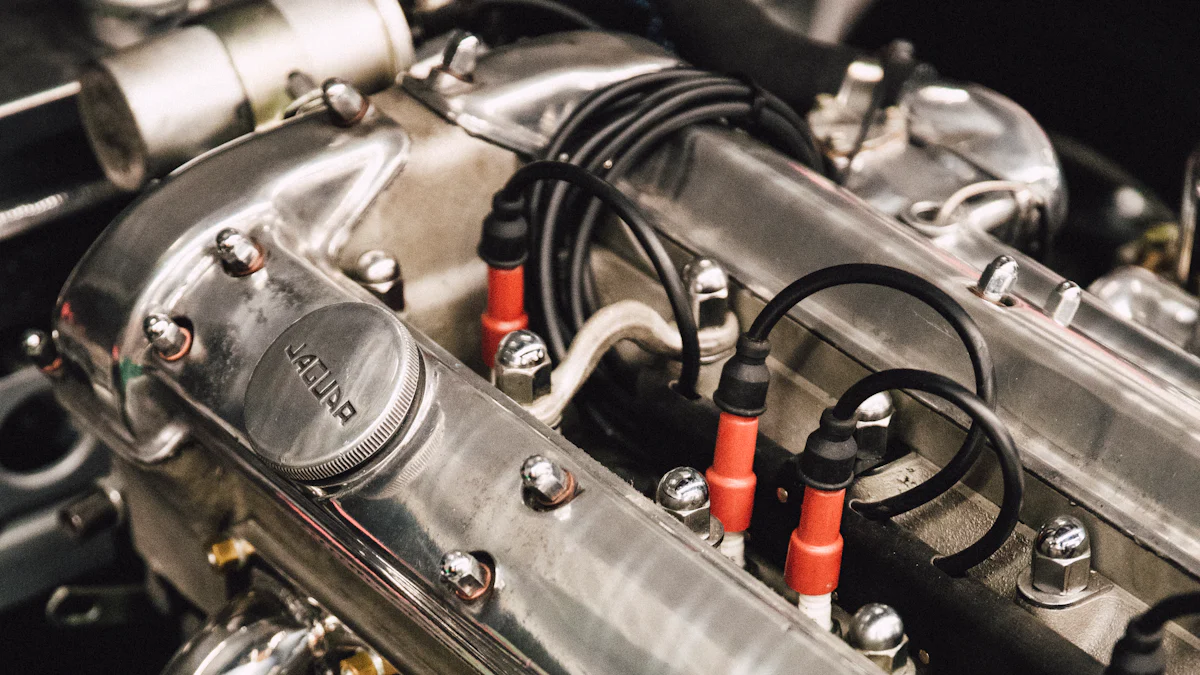
Understanding Exhaust Manifolds
Types of Exhaust Manifolds
Cast Iron Manifolds
Cast iron manifolds offer durability and cost-effectiveness. These manifolds withstand high temperatures and resist cracking. However, their heavy weight can negatively impact vehicle performance. Cast iron manifolds often appear in older or budget-conscious vehicle models.
Stainless Steel Manifolds
Stainless steel manifolds provide a balance between strength and weight. These manifolds resist corrosion and maintain structural integrity under extreme conditions. The lighter weight of stainless steel improves overall vehicle efficiency. Many modern vehicles utilize stainless steel manifolds for enhanced performance.
Tubular Manifolds
Tubular manifolds, also known as headers, consist of individual pipes for each cylinder. These pipes converge into a single collector. Tubular manifolds optimize exhaust gas flow and reduce backpressure. Performance enthusiasts often prefer tubular manifolds for their ability to boost power output.
Function and Design
Role in Engine Efficiency
The exhaust manifold plays a critical role in engine efficiency. Proper design ensures smooth exhaust gas flow from the engine cylinders to the exhaust system. Efficient gas flow minimizes backpressure, which enhances engine performance and fuel economy. The exhaust manifold also helps manage engine temperature by directing hot gases away from the engine block.
Design Considerations
Designing an exhaust manifold involves several key considerations. Engineers must account for the shape and length of the manifold pipes. Proper pipe length and diameter ensure optimal gas flow and minimize turbulence. The manifold must also fit within the engine bay without interfering with other components. Additionally, the design should facilitate easy installation and maintenance.
Material Selection
Material selection significantly impacts the performance of an exhaust manifold. High-quality materials withstand thermal and mechanical stresses. Cast iron, stainless steel, and tubular designs each offer unique benefits. Cast iron provides durability, while stainless steel offers a balance of strength and weight. Tubular manifolds enhance performance through optimized gas flow. Engineers must choose the appropriate material based on the specific requirements of the vehicle.
Emissions Analysis
Types of Emissions
Carbon Monoxide (CO)
Carbon monoxide forms during incomplete combustion of fuel. This gas poses significant health risks, including headaches and dizziness. The exhaust manifold must efficiently channel exhaust gases to minimize CO emissions. Proper design and material selection play crucial roles in reducing CO levels.
Hydrocarbons (HC)
Hydrocarbons result from unburned fuel escaping the combustion chamber. These compounds contribute to smog and respiratory issues. The exhaust manifold’s design impacts the engine’s ability to burn fuel completely. Optimized designs help reduce HC emissions by ensuring efficient exhaust gas flow.
Nitrogen Oxides (NOx)
Nitrogen oxides form at high combustion temperatures. These gases cause environmental and health problems, including acid rain and respiratory ailments. The exhaust manifold influences NOx emissions through temperature management. Effective designs help maintain lower combustion temperatures, thereby reducing NOx formation.
Impact of Exhaust Manifold on Emissions
Design Influence
The design of the exhaust manifold directly affects emissions. A well-designed manifold ensures smooth exhaust gas flow, reducing backpressure and improving combustion efficiency. Studies show that tapered designs enhance performance by decreasing backpressure. Improved gas flow leads to lower emissions of CO, HC, and NOx.
Material Influence
Material selection significantly impacts the exhaust manifold’s performance. Cast iron and stainless steel are common materials used in manifold construction. Cast iron offers durability but may increase weight. Stainless steel provides a balance between strength and weight, enhancing overall efficiency. Both materials must withstand thermal and mechanical stresses to maintain optimal performance and reduce emissions.
Temperature Management
Temperature management plays a crucial role in controlling emissions. The exhaust manifold must effectively dissipate heat to prevent excessive combustion temperatures. High temperatures lead to increased NOx formation. Efficient temperature management helps maintain lower combustion temperatures, thereby reducing NOx emissions. Advanced materials and coatings can further enhance the manifold’s ability to manage heat.
Power Output Analysis
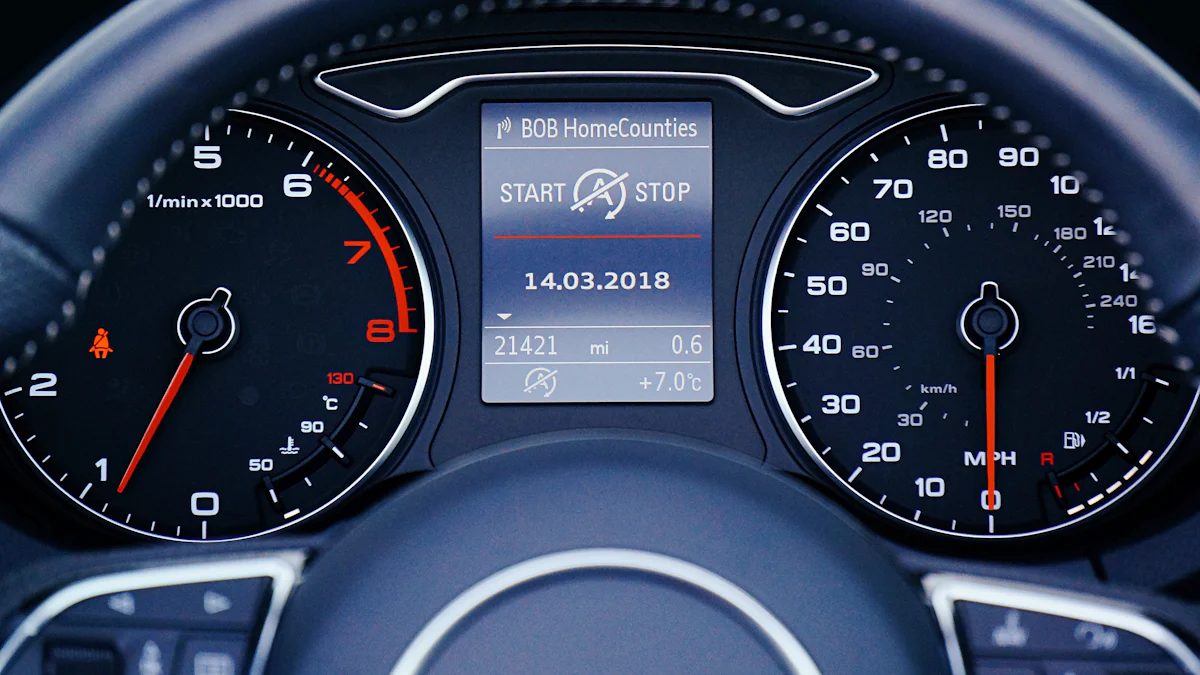
Factors Affecting Power Output
Exhaust Flow Dynamics
Exhaust flow dynamics play a critical role in engine performance. The design of the exhaust manifold directly influences how efficiently exhaust gases exit the engine. A well-designed manifold ensures smooth and rapid gas flow, reducing turbulence. This results in improved engine breathing and enhanced power output. Engineers often optimize the shape and length of the manifold pipes to achieve ideal flow characteristics.
Backpressure
Backpressure refers to the resistance that exhaust gases encounter as they exit the engine. High backpressure can hinder engine performance by restricting exhaust flow. Performance exhaust headers aim to decrease flow resistance, thereby increasing the engine’s volumetric efficiency. Lower backpressure allows the engine to expel exhaust gases more effectively, leading to a gain in power output. The newly constructed exhaust manifold designs often focus on minimizing backpressure to boost engine performance.
Heat Retention
Heat retention within the exhaust manifold affects engine efficiency and power output. Excessive heat can lead to higher combustion temperatures, which may reduce engine performance. Efficient heat management helps maintain optimal operating temperatures. Advanced materials and coatings in the manifold construction can enhance heat dissipation. Proper heat retention ensures that the engine operates within its ideal temperature range, maximizing power output.
Performance Testing
Dyno Testing
Dyno testing provides a controlled environment to measure the performance of an exhaust manifold. Engineers use a dynamometer to simulate real-world driving conditions. This testing method evaluates the impact of the manifold on power output, torque, and fuel efficiency. Dyno testing offers precise data, enabling engineers to make informed decisions about manifold design and material selection.
Real-world Testing
Real-world testing complements dyno testing by evaluating the exhaust manifold under actual driving conditions. Engineers assess how the manifold performs in various scenarios, such as city driving, highway cruising, and aggressive acceleration. Real-world testing helps identify any potential issues that may not appear in a controlled environment. This comprehensive approach ensures that the exhaust manifold delivers consistent performance across different driving conditions.
Comparative Analysis
Comparative analysis involves evaluating different exhaust manifold designs to determine their impact on power output. Engineers compare factors such as exhaust flow dynamics, backpressure, and heat retention. This analysis helps identify the most effective designs for enhancing engine performance. By comparing various manifolds, engineers can pinpoint the strengths and weaknesses of each design. This process leads to continuous improvement and innovation in exhaust manifold technology.
Innovations and Future Trends
Advanced Materials
Ceramic Coatings
Ceramic coatings have emerged as a significant advancement in exhaust manifold technology. These coatings provide excellent thermal insulation, reducing heat transfer to surrounding engine components. This insulation helps maintain optimal engine temperatures, enhancing performance and longevity. Ceramic coatings also offer superior resistance to corrosion and wear, ensuring the durability of the exhaust manifold. Automotive engineers increasingly adopt ceramic coatings to improve the efficiency and reliability of exhaust systems.
Composite Materials
Composite materials represent another innovative approach in exhaust manifold design. These materials combine different substances to achieve a balance of strength, weight, and thermal resistance. For example, carbon fiber composites offer high strength-to-weight ratios, making them ideal for performance applications. The use of composite materials can significantly reduce the weight of the exhaust manifold, leading to improved vehicle efficiency and handling. The FluidForming Lightweight Stainless Steel Exhaust Manifold Case Study demonstrated the successful replacement of heavy cast iron manifolds with lightweight stainless steel, highlighting the benefits of advanced materials in automotive engineering.
Design Innovations
Variable Geometry Manifolds
Variable geometry manifolds (VGM) represent a cutting-edge innovation in exhaust manifold design. VGMs adjust the shape and length of the manifold pipes based on engine operating conditions. This adaptability optimizes exhaust gas flow, reducing backpressure and enhancing engine performance. VGMs can improve fuel efficiency and reduce emissions by maintaining optimal exhaust dynamics across various driving scenarios. Automotive manufacturers increasingly explore VGMs to meet stringent emission regulations and performance demands.
Integrated Catalytic Converters
Integrating catalytic converters directly into the exhaust manifold offers several advantages. This design reduces the distance that exhaust gases travel before reaching the catalytic converter, improving the efficiency of emission control. Integrated catalytic converters help achieve faster light-off times, reducing cold start emissions. This integration also simplifies the exhaust system layout, reducing weight and complexity. Many modern vehicles now feature integrated catalytic converters to meet environmental standards while maintaining high performance.
The analysis highlights the critical role of exhaust manifold design and material selection in optimizing engine performance and reducing emissions. Key findings indicate that advanced materials like stainless steel and ceramic coatings enhance durability and efficiency. Design innovations such as variable geometry manifolds and integrated catalytic converters improve fuel efficiency and emission control.
Technological advancements and changing consumer preferences drive significant implications for the automotive industry. Efficient exhaust systems and driving practices can mitigate vehicle emissions, contributing to environmental sustainability. Future research should focus on developing lightweight materials and innovative designs to meet evolving regulatory and performance demands.
Post time: Jul-31-2024