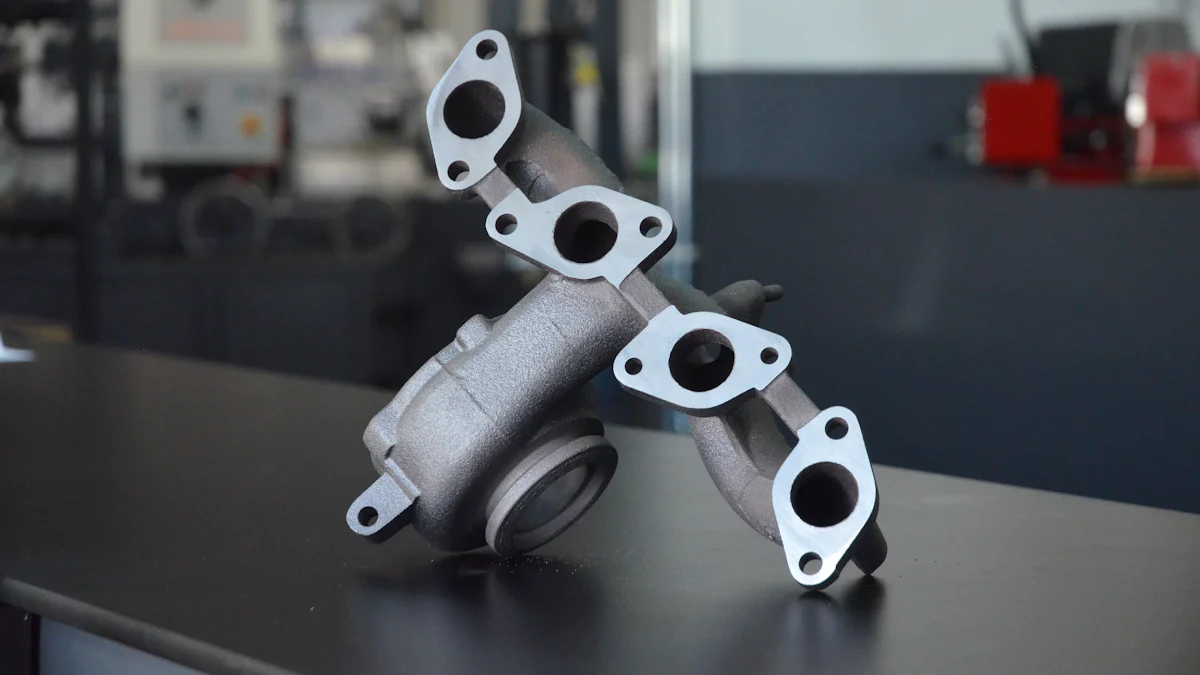
An exhaust manifold serves as a crucial component in a vehicle’s exhaust system. This part collects exhaust gases from the engine’s cylinders and channels them into the exhaust pipe. Selecting the appropriate exhaust manifold type significantly impacts engine performance, fuel efficiency, and emission control. Various designs and materials cater to different needs, from enhancing power in high-performance cars to meeting stringent pollution laws in regular vehicles.
Cast Iron Exhaust Manifolds
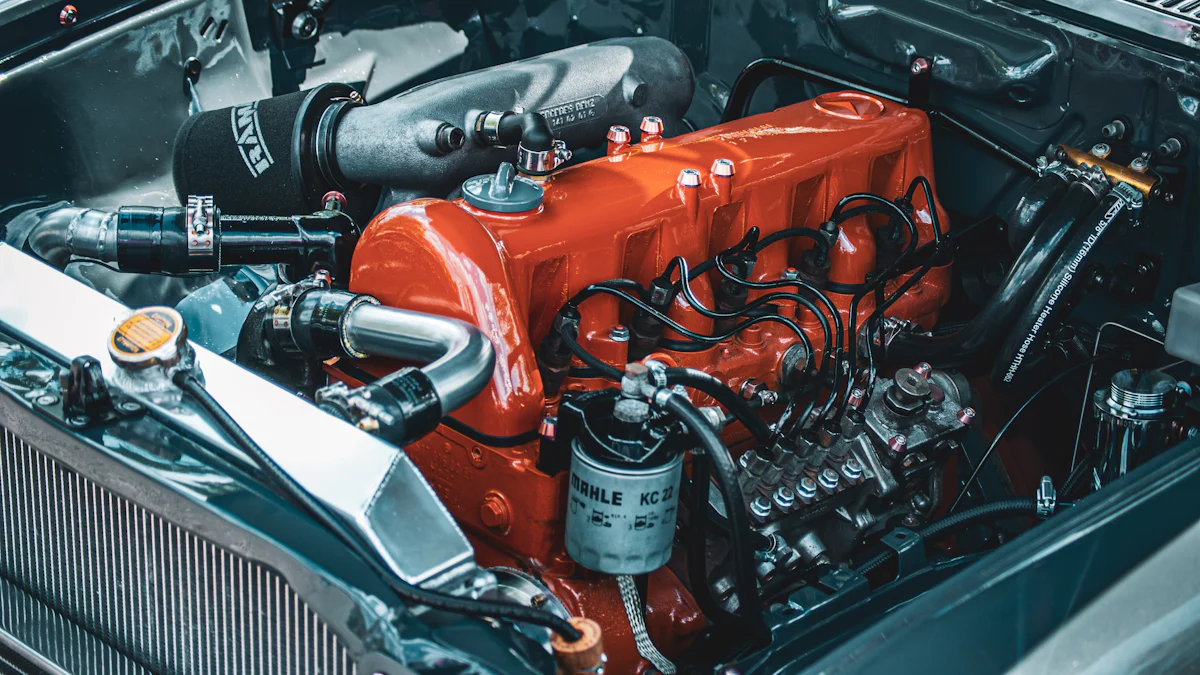
Overview of Cast Iron Exhaust Manifolds
What are Cast Iron Exhaust Manifolds?
Cast iron exhaust manifolds serve as a critical component in many vehicles. These manifolds collect exhaust gases from the engine’s cylinders and direct them into the exhaust system. Manufacturers often use cast iron due to its durability and cost-effectiveness. The design typically features short, unequal pathways that converge into a single collector.
Common Applications of Cast Iron Exhaust Manifolds
Most original equipment manufacturers (OEMs) use cast iron exhaust manifolds in regular production vehicles. These manifolds are common in cars, trucks, and SUVs due to their robustness and ability to withstand high temperatures. Cast iron manifolds also find applications in diesel engines, where they help improve performance by managing exhaust gas flow.
Pros of Cast Iron Exhaust Manifolds
Durability
Cast iron exhaust manifolds offer exceptional durability. The material can withstand high temperatures and harsh conditions without deforming or cracking. This makes cast iron an ideal choice for vehicles that require long-lasting components.
Cost-Effectiveness
The cost-effectiveness of cast iron exhaust manifolds makes them popular among manufacturers. Producing these manifolds involves relatively low costs compared to other materials like stainless steel or titanium. This affordability allows manufacturers to keep vehicle prices competitive while ensuring reliable performance.
Cons of Cast Iron Exhaust Manifolds
Weight
One significant drawback of cast iron exhaust manifolds is their weight. Cast iron is much heavier than alternative materials like stainless steel or aluminum. This added weight can negatively impact vehicle performance and fuel efficiency.
Heat Retention
Cast iron exhaust manifolds tend to retain heat more than other materials. This heat retention can lead to higher engine bay temperatures, which may affect other components. Additionally, excessive heat can contribute to the formation of cracks over time, reducing the manifold’s lifespan.
Stainless Steel Exhaust Manifolds
Overview of Stainless Steel Exhaust Manifolds
What are Stainless Steel Exhaust Manifolds?
Stainless steel exhaust manifolds serve as an advanced alternative to traditional cast iron manifolds. These manifolds collect exhaust gases from the engine’s cylinders and direct them into the exhaust system. Manufacturers use stainless steel due to its superior properties, including resistance to rust and corrosion. The design often features equal-length pathways, which help optimize exhaust flow and improve engine performance.
Common Applications of Stainless Steel Exhaust Manifolds
High-performance vehicles frequently use stainless steel exhaust manifolds. These manifolds also find applications in sports cars and luxury vehicles, where performance and aesthetics are crucial. Many aftermarket parts manufacturers offer stainless steel manifolds as upgrades for enthusiasts looking to enhance their vehicle’s performance and longevity.
Pros of Stainless Steel Exhaust Manifolds
Corrosion Resistance
Stainless steel exhaust manifolds offer excellent resistance to corrosion. This material can withstand harsh environmental conditions without rusting, making it ideal for vehicles exposed to moisture and road salt. Corrosion resistance ensures a longer lifespan compared to other materials.
Weight Reduction
Stainless steel exhaust manifolds are significantly lighter than cast iron counterparts. The reduced weight contributes to better vehicle performance and fuel efficiency. Lightweight components also reduce the overall strain on the engine, leading to improved longevity and reliability.
Cons of Stainless Steel Exhaust Manifolds
Cost
The primary drawback of stainless steel exhaust manifolds is their cost. Manufacturing these manifolds involves higher expenses due to the material’s properties and the complexity of the production process. This increased cost makes stainless steel manifolds less accessible for budget-conscious consumers.
Potential for Cracking
Stainless steel exhaust manifolds, while durable, have a potential for cracking under extreme conditions. Rapid temperature changes and high-stress environments can cause stainless steel to develop cracks over time. Proper installation and maintenance can mitigate this risk, but it remains a consideration for users.
Tubular Headers
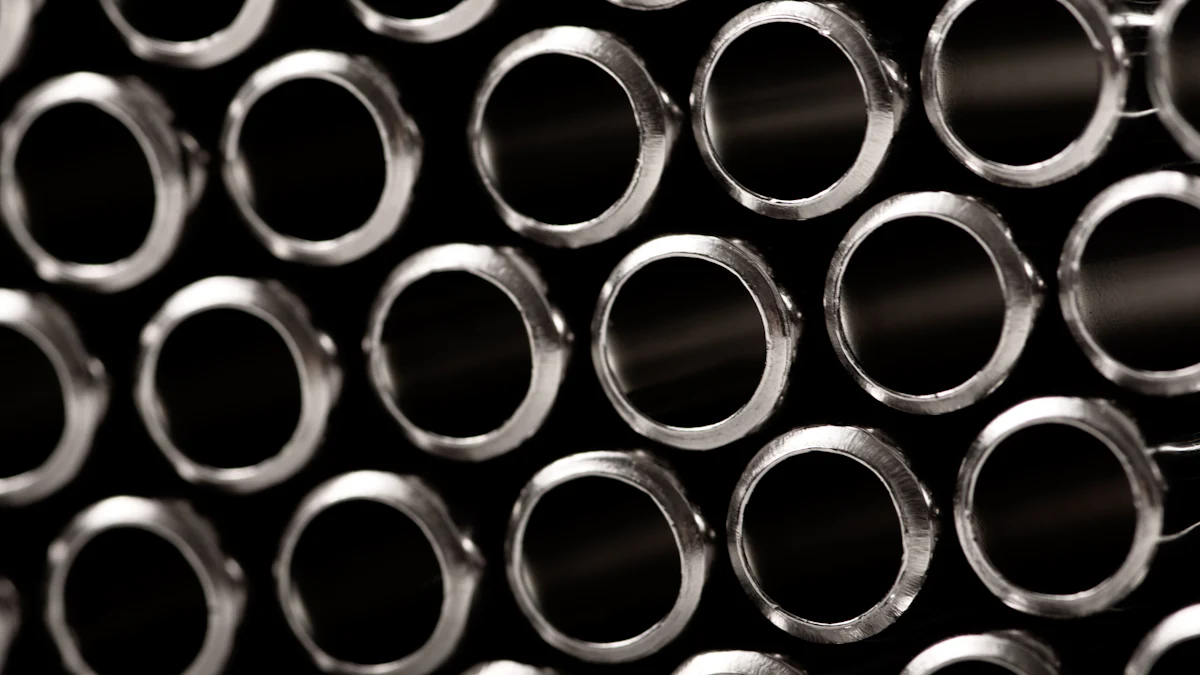
Overview of Tubular Headers
What are Tubular Headers?
Tubular headers, also known as exhaust headers, consist of individual tubes that connect each engine cylinder to a single collector pipe. These headers aim to optimize the flow of exhaust gases, reducing back pressure and enhancing engine performance. Manufacturers often use materials like steel, stainless steel, titanium, or Inconel to construct tubular headers. The design typically features equal-length tubes to ensure uniform exhaust gas flow from each cylinder.
Common Applications of Tubular Headers
High-performance vehicles frequently utilize tubular headers to maximize power output. These headers also find applications in sports cars and racing vehicles where every bit of performance gain matters. Many automotive enthusiasts opt for tubular headers as aftermarket upgrades to improve their vehicle’s horsepower and torque.
Pros of Tubular Headers
Performance Improvement
Tubular headers offer significant performance improvements by reducing back pressure in the exhaust system. This reduction allows the engine to breathe more easily, resulting in increased horsepower and torque. Studies have shown that long-tube headers, in particular, provide smoother exhaust flow compared to short-tube headers, further enhancing performance. Headers also contribute to better engine tuning, allowing for longer duration and increased overlap in cam tuning.
Weight Reduction
Tubular headers are generally lighter than traditional cast iron exhaust manifolds. This weight reduction contributes to improved vehicle performance and fuel efficiency. Lightweight components place less strain on the engine, leading to enhanced longevity and reliability. Stainless steel and titanium headers offer additional weight savings without compromising durability.
Cons of Tubular Headers
Cost
The primary drawback of tubular headers is their cost. Manufacturing these headers involves higher expenses due to the materials used and the complexity of the design. High-quality materials like stainless steel and titanium add to the overall cost, making tubular headers less accessible for budget-conscious consumers. Despite the higher price, many enthusiasts consider the performance gains worth the investment.
Installation Complexity
Installing tubular headers can be more complex compared to traditional exhaust manifolds. The intricate design and precise fitment requirements often necessitate professional installation. Improper installation can lead to exhaust leaks and reduced performance. Additionally, packaging constraints in the engine bay can pose challenges during installation. Proper planning and expertise are essential to ensure optimal performance and longevity of tubular headers.
Ceramic Coated Headers
Overview of Ceramic Coated Headers
What are Ceramic Coated Headers?
Ceramic coated headers feature a layer of ceramic material applied to the surface of traditional exhaust headers. This coating serves multiple purposes, including enhancing heat resistance and improving durability. Manufacturers use advanced techniques to bond the ceramic layer to the metal substrate, ensuring a robust and long-lasting finish. The ceramic coating can withstand extreme temperatures, making it ideal for high-performance applications.
Common Applications of Ceramic Coated Headers
High-performance vehicles often utilize ceramic coated headers to manage heat more effectively. These headers also find applications in racing cars and modified street vehicles where optimal performance is crucial. Many automotive enthusiasts choose ceramic coated headers as aftermarket upgrades to enhance both the performance and appearance of their exhaust systems.
Pros of Ceramic Coated Headers
Heat Management
Ceramic coated headers excel in heat management. The ceramic layer acts as an insulator, reducing the amount of heat radiated from the exhaust system. This helps maintain lower engine bay temperatures, which can protect other components from heat damage. Improved heat management also contributes to better overall engine performance.
Durability
The durability of ceramic coated headers surpasses that of uncoated headers. The ceramic layer provides a protective barrier against corrosion and wear. This makes the headers more resistant to the harsh conditions they encounter during operation. The coating can also withstand thermal shock, preventing cracks and chips even under extreme temperature fluctuations.
Cons of Ceramic Coated Headers
Cost
The cost of ceramic coated headers represents a significant drawback. The process of applying the ceramic coating involves specialized equipment and materials, which increases production expenses. This makes ceramic coated headers more expensive than their uncoated counterparts. Budget-conscious consumers may find these headers less accessible due to the higher price point.
Potential for Coating Damage
Ceramic coated headers face the potential for coating damage. The ceramic layer, while durable, can suffer from chipping or cracking if subjected to physical impacts or improper handling. Repairing damaged coatings can be challenging and may require professional intervention. Ensuring proper installation and maintenance can help mitigate the risk of coating damage.
Exhaust manifolds come in various types, each with unique advantages and disadvantages.
- Cast Iron Exhaust Manifolds:
- Pros: Durability, cost-effectiveness
- Cons: Weight, heat retention
- Stainless Steel Exhaust Manifolds:
- Pros: Corrosion resistance, weight reduction
- Cons: Cost, potential for cracking
- Tubular Headers:
- Pros: Performance improvement, weight reduction
- Cons: Cost, installation complexity
- Ceramic Coated Headers:
- Pros: Heat management, durability
- Cons: Cost, potential for coating damage
Choosing the right exhaust manifold depends on specific needs and goals. High-performance applications may benefit from tubular or ceramic coated headers. Budget-conscious consumers may prefer cast iron or stainless steel options. Selecting the appropriate design optimizes engine performance and longevity.
Post time: Jul-23-2024