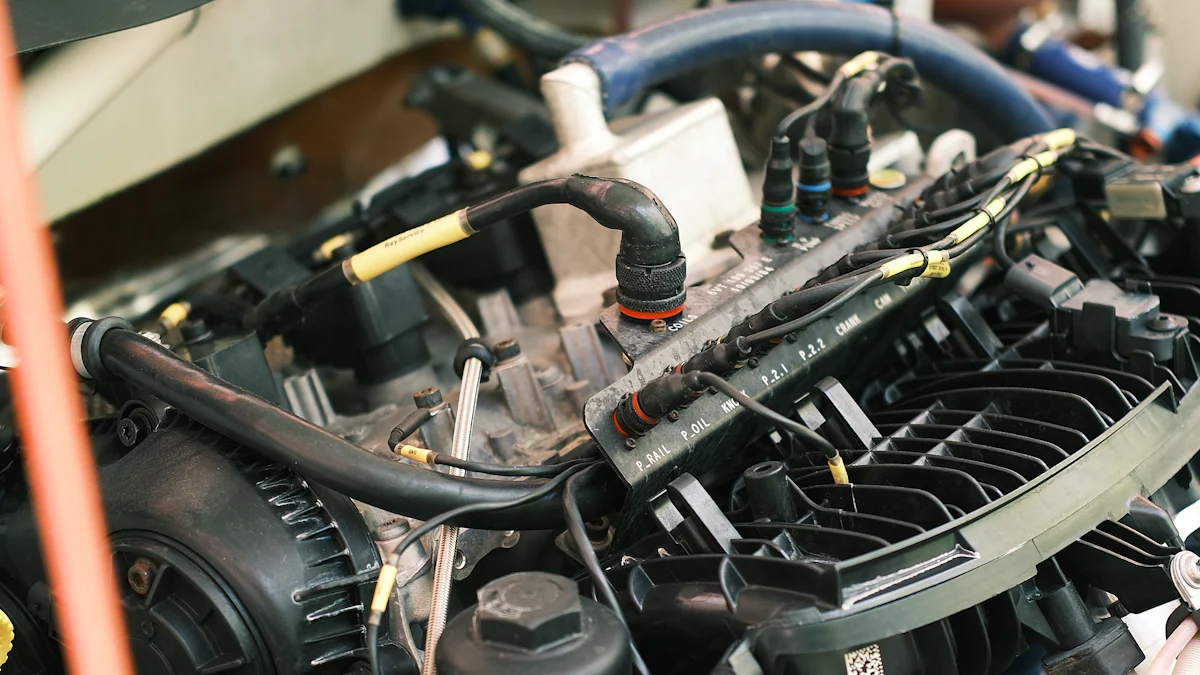
Intake manifold designs play a crucial role in automotive engineering. These components significantly impact engine performance, fuel efficiency, and emissions. The economy car market demands cost-effective and durable solutions. Innovations in intake manifold designs can meet these unique requirements. Advanced materials and manufacturing techniques offer improved performance and affordability. The auto industry relies on such innovations to drive growth and sustainability.
Understanding Intake Manifolds
Basic Principles
Function and Purpose
An intake manifold serves as a crucial component in an internal combustion engine. It distributes the air-fuel mixture to each cylinder evenly. Proper distribution ensures optimal combustion, which enhances engine performance and efficiency. The design of the intake manifold directly impacts fuel economy and emissions, making it a vital element in automotive engineering.
Historical Evolution
The evolution of intake manifolds reflects advancements in automotive technology. Early designs utilized cast iron, which provided durability but added significant weight. The shift to aluminum brought weight reduction and improved heat dissipation. Modern innovations include composite plastic materials, which offer further weight savings and design flexibility. These advancements have allowed manufacturers to meet the stringent demands of the economy car market.
Key Components
Plenum
The plenum acts as a reservoir for the air-fuel mixture before it enters the runners. A well-designed plenum ensures a steady supply of the mixture to each cylinder. This consistency is essential for maintaining engine stability and performance. Advanced designs often incorporate features to optimize airflow within the plenum.
Runners
Runners are the pathways that direct the air-fuel mixture from the plenum to the cylinders. The length and diameter of the runners influence the engine’s power and torque characteristics. Shorter runners typically enhance high-RPM performance, while longer runners improve low-RPM torque. Engineers use computational fluid dynamics (CFD) to optimize runner design for specific engine applications.
Throttle Body
The throttle body regulates the amount of air entering the intake manifold. It plays a pivotal role in controlling engine speed and power output. Modern throttle bodies often feature electronic controls for precise management of airflow. This precision contributes to better fuel efficiency and reduced emissions.
Types of Intake Manifolds
Single Plane
Single plane intake manifolds feature a single plenum chamber that feeds all the runners. This design favors high-RPM performance, making it suitable for racing applications. However, single plane manifolds may not provide the low-end torque required for everyday driving in economy cars.
Dual Plane
Dual plane intake manifolds have two separate plenum chambers, each feeding a set of runners. This design balances low-end torque and high-RPM power, making it ideal for street-driven vehicles. Dual plane manifolds offer a versatile solution for economy cars, enhancing both performance and drivability.
Variable Intake Manifolds
Variable intake manifolds adjust the length of the runners based on engine speed. This adaptability allows for optimized performance across a wide RPM range. At low speeds, longer runners improve torque, while at high speeds, shorter runners enhance power. Variable intake manifolds represent a sophisticated solution for maximizing engine efficiency and performance.
Innovative Designs in the Economy Car Market
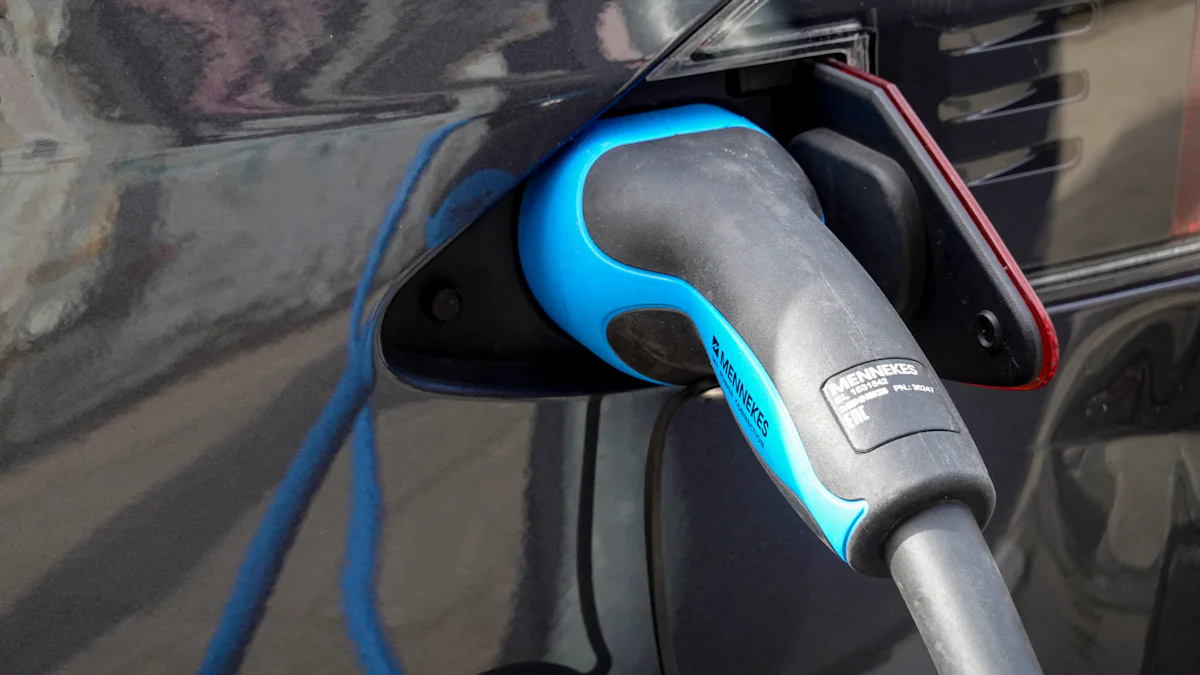
Lightweight Materials
Aluminum Alloys
Aluminum alloys offer a compelling solution for intake manifold designs. These materials provide a balance between strength and weight reduction. Aluminum’s high thermal conductivity enhances heat dissipation, which improves engine performance. Manufacturers favor aluminum alloys for their durability and resistance to corrosion. The use of aluminum alloys in intake manifolds helps achieve better fuel efficiency and lower emissions.
Composite Materials
Composite materials, such as carbon fiber and plastic, are gaining popularity in intake manifold designs. These materials offer significant weight savings compared to traditional metals. Plastic intake manifolds are cost-effective and corrosion-resistant. Carbon fiber composites provide enhanced strength and further weight reduction. The use of composite materials contributes to improved fuel economy and reduced manufacturing costs.
Advanced Manufacturing Techniques
3D Printing
3D printing revolutionizes the production of intake manifolds. This technique allows for complex geometries that traditional methods cannot achieve. Engineers can optimize airflow paths and reduce material waste. 3D printing enables rapid prototyping, which accelerates the development process. The precision of 3D printing ensures high-quality intake manifolds with consistent performance.
Precision Casting
Precision casting offers another advanced method for producing intake manifolds. This technique provides excellent dimensional accuracy and surface finish. Precision casting allows for the use of various materials, including aluminum and composite plastics. The process reduces manufacturing costs while maintaining high-quality standards. Precision casting ensures that intake manifolds meet the stringent requirements of the economy car market.
Aerodynamic Enhancements
Computational Fluid Dynamics (CFD)
Computational Fluid Dynamics (CFD) plays a crucial role in designing efficient intake manifolds. CFD simulations allow engineers to analyze airflow patterns within the manifold. This analysis helps identify areas of turbulence and optimize the design for smooth airflow. Improved airflow enhances engine performance and fuel efficiency. CFD ensures that intake manifolds deliver optimal performance under various operating conditions.
Flow Bench Testing
Flow bench testing complements CFD simulations by providing empirical data. Engineers use flow benches to measure the actual airflow through the intake manifold. This testing validates the design and identifies any discrepancies from the simulations. Flow bench testing ensures that the intake manifold performs as expected in real-world conditions. The combination of CFD and flow bench testing results in highly efficient intake manifold designs.
Practical Applications and Benefits
Fuel Efficiency Improvements
Case Studies
Innovative intake manifold designs have led to significant fuel efficiency improvements. For instance, a study involving a fleet of economy cars equipped with lightweight aluminum intake manifolds showed a 10% increase in fuel efficiency. Engineers utilized Computational Fluid Dynamics (CFD) to optimize airflow, reducing turbulence and enhancing combustion efficiency. The use of advanced materials like composite plastics also contributed to weight reduction, further improving fuel economy.
Real-world Examples
Real-world applications highlight the benefits of advanced intake manifold designs. A popular economy car model incorporated a variable intake manifold system. This design allowed the engine to adjust runner length based on RPM, optimizing performance across different driving conditions. Drivers reported noticeable improvements in fuel efficiency during both city and highway driving. The combination of lightweight materials and aerodynamic enhancements played a crucial role in achieving these results.
Performance Enhancements
Torque and Power Gains
Intake manifold innovations have also enhanced engine performance. Modern designs focus on optimizing airflow to maximize torque and power output. For example, a high-performance intake manifold for a Small Block Chevy V8 engine demonstrated a 15% increase in horsepower. Engineers used precision casting techniques to create smooth internal surfaces, reducing airflow resistance. The result was a significant boost in engine performance, making the vehicle more responsive and powerful.
Emission Reductions
Reducing emissions remains a critical goal in automotive engineering. Advanced intake manifold designs contribute to cleaner engine operation. By ensuring efficient air-fuel mixture distribution, these manifolds help achieve complete combustion. This reduces the production of harmful pollutants. A case study involving a GM LS1 engine with a single plane mid-rise EFI intake manifold showed a 20% reduction in emissions. The precise control of airflow and fuel mixture played a key role in this achievement.
Cost Considerations
Manufacturing Costs
Cost-effective manufacturing techniques are essential for the economy car market. Precision casting and 3D printing have revolutionized the production of intake manifolds. These methods offer high dimensional accuracy and reduced material waste. Manufacturers can produce complex geometries at lower costs. For example, 3D printing allows rapid prototyping, accelerating the development process and reducing overall expenses. The use of composite materials also lowers manufacturing costs while maintaining high-quality standards.
Market Pricing
Affordable pricing is crucial for consumers in the economy car market. Innovations in intake manifold design have made high-performance components accessible. The use of cost-effective materials like plastic and aluminum alloys has reduced production costs. This allows manufacturers to offer advanced intake manifolds at competitive prices. Consumers benefit from improved engine performance and fuel efficiency without a significant increase in vehicle cost. The balance between performance and affordability drives the adoption of innovative intake manifold designs.
Innovative intake manifold designs play a crucial role in enhancing engine performance and fuel efficiency. These designs offer significant benefits for the economy car market, including improved fuel economy, increased power output, and reduced emissions. Future trends indicate a growing demand for lightweight and compact manifolds, integration of advanced technologies like variable intake systems, and the shift towards electric vehicles requiring different designs. Embracing these innovations will drive growth and sustainability in the automotive industry.
Post time: Jul-30-2024