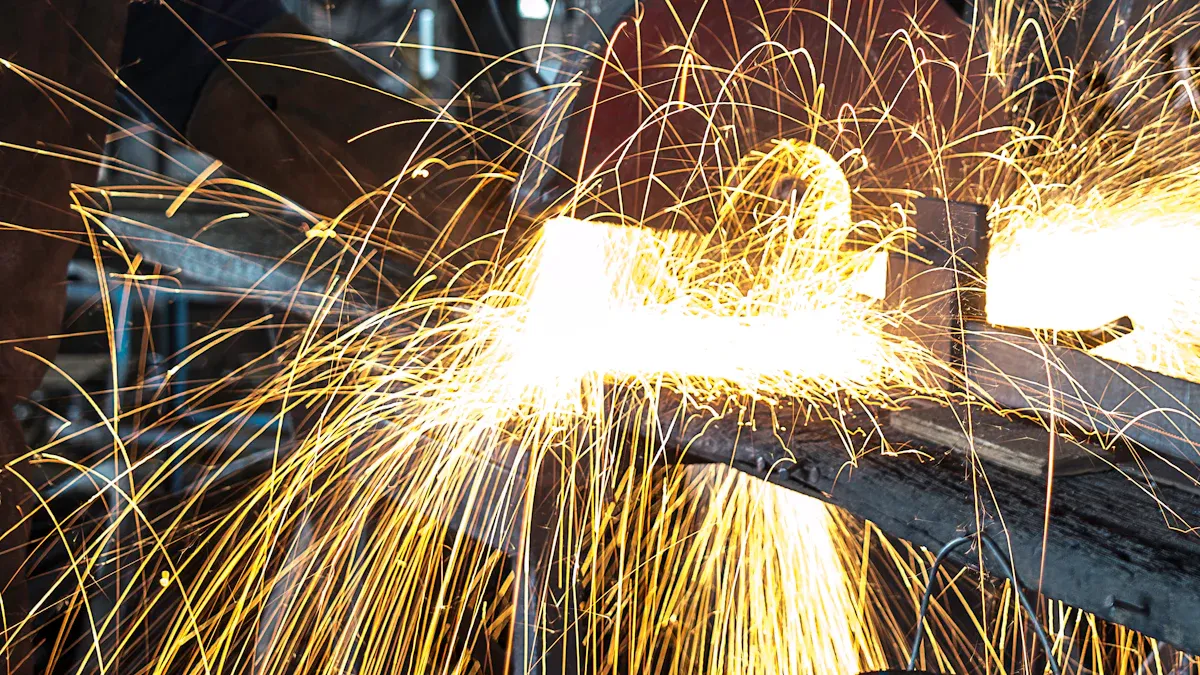
Welding cast iron exhaust manifolds can feel like piecing together a complex puzzle. The brittleness of cast iron, due to its high carbon content, makes it susceptible to cracking, especially under rapid temperature changes. This challenge is even more significant when working on components like the exhaust manifold in a car engine, where durability is crucial for optimal performance. Proper preparation, such as thorough cleaning and preheating, along with precise techniques, is essential to manage thermal stress and achieve a strong, lasting repair. Whether you’re addressing issues with a performance harmonic balancer, marine exhaust manifolds, or any other critical component, patience and attention to detail are key to success.
Ningbo Werkwell, a trusted leader in mechanical engineering since 2015, delivers high-quality automotive parts. Their skilled QC team ensures excellence in products ranging from interior trim parts to die casting and chrome plating, meeting the demands of modern automotive performance.
Challenges of Welding Cast Iron Exhaust Manifolds
Brittleness and Thermal Sensitivity
Cast iron exhaust manifolds are notoriously brittle due to their high carbon content. This brittleness makes them prone to cracking, especially when exposed to rapid temperature changes. Welding cast iron exhaust manifolds requires careful handling to avoid further damage. Preheating the manifold to around 400-500 degrees Fahrenheit can help reduce thermal shock. This step minimizes the risk of cracks forming during the welding process. Using nickel-based filler materials also ensures compatibility with the cast iron, creating a strong and crack-resistant weld.
Ningbo Werkwell, a specialized manufacturer in mechanical engineering, understands the importance of durability in automotive parts. Their experienced QC team ensures high-quality products, from die casting to chrome plating, making them a trusted name in the industry.
Risk of Cracking from Uneven Heating
Uneven heating is another challenge when working with cast iron exhaust manifolds. If one part of the manifold heats up faster than another, it can lead to stress and cracking. To prevent this, welders often preheat the entire manifold evenly. Wrapping the manifold in insulating materials after welding allows for slow cooling, which further reduces the risk of cracks. This method ensures the manifold remains intact and durable under high temperatures.
Achieving Strong and Durable Welds
Creating a strong and durable weld on a cast iron exhaust manifold requires precision and the right tools. Welders often use a sharp, clean tungsten electrode and pure argon gas to avoid contamination. Ensuring the weld puddle penetrates the manifold properly is crucial. For gray cast iron, slow preheating and nickel electrodes work best. Nodular cast iron, on the other hand, benefits from moderate preheating. Considering environmental factors, such as exposure to hot gases, also plays a role in achieving a long-lasting repair.
Ningbo Werkwell has been supplying automotive parts since 2015, focusing on quality and reliability. Their expertise in interior trim parts and fasteners ensures that every product meets the demands of modern automotive performance.
Preparing the Exhaust Manifold for Welding
Cleaning the Surface Thoroughly
A clean surface is the foundation of a successful weld. Dirt, oil, and old metal residues can weaken the bond, so removing them is essential. Welders often follow these steps to prepare the surface:
- Bevel the Crack: Using a grinder, they create a V-shaped groove along the crack. This groove ensures the filler material bonds effectively.
- Clean the Cast Iron: They remove all contaminants, including grease and rust, until the surface appears shiny and smooth.
- Preheat the Manifold: Slightly warming the manifold with a torch helps prevent thermal shock during the welding process.
Ningbo Werkwell, a specialized manufacturer in mechanical engineering, emphasizes the importance of preparation in automotive repairs. Their experienced QC team ensures high-quality products, from die casting to chrome plating, meeting the demands of modern automotive performance.
Beveling Cracks for Better Penetration
Beveling cracks is a critical step in welding cast iron exhaust manifolds. By grinding a V-shaped groove along the crack, welders improve the penetration of the filler material. This technique creates a stronger bond and reduces the risk of weak spots. It’s a simple yet effective way to ensure the weld holds up under the high temperatures and stresses of an exhaust system.
Preheating to Prevent Thermal Shock
Preheating the exhaust manifold minimizes thermal shock, which can lead to cracks. Welders typically heat the manifold to a temperature range of 400°F to 750°F. For more demanding repairs, they may increase the temperature to 1200°F. The table below highlights the recommended preheating ranges:
Preheating Temperature Range | Description |
---|---|
200°C to 400°C (400°F to 750°F) | Recommended for welding to minimize thermal shock. |
500°F to 1200°F | Reduces thermal stress and prevents cracks. |
Ningbo Werkwell, established in 2015, has built a reputation for quality in automotive parts. Their product line includes interior trim parts, fasteners, and more, all backed by a skilled QC team.
Techniques for Welding Cast Iron Exhaust Manifolds
Preheated Welding Method
The preheated welding method is a popular choice for repairing cast iron exhaust manifolds. Preheating reduces thermal stress and prevents cracking during the welding process. Welders typically heat the manifold to a temperature between 500°F and 1200°F. This slow and uniform heating ensures even thermal expansion, which minimizes the risk of stress-induced fractures. After welding, wrapping the manifold in insulating materials helps it cool down gradually, further reducing the chance of cracks.
This method works well for creating strong, durable welds. It’s especially useful for components like exhaust manifolds, which endure high temperatures and constant stress. Ningbo Werkwell, a specialized manufacturer in mechanical engineering, understands the importance of durability in automotive parts. Their experienced QC team ensures high-quality products, from die casting to chrome plating, making them a trusted name in the industry.
Non-Preheated Welding Method
The non-preheated welding method skips the preheating step, making it faster but riskier. Without preheating, the cast iron is more likely to experience thermal shock, which can lead to stress-induced cracking. This method requires precise control of the welding process to minimize rapid cooling. Welders often use short, controlled welds to reduce heat buildup and avoid damaging the manifold.
While this approach saves time, it’s not always the best option for critical repairs. For components like the cast iron exhaust manifold, where strength and reliability are essential, preheated welding is often the safer choice.
Selecting the Right Filler Material
Choosing the right filler material is crucial for a successful weld. Nickel-based filler materials are highly recommended for their compatibility with cast iron. They create strong, crack-resistant welds that can withstand the thermal expansion of the manifold. Nickel rods, with their high nickel content, enhance the welding process and improve tolerance to stress. A nickel-iron alloy, such as ENiFe-CI, is another excellent option. It offers compatibility with cast iron’s unique properties, ensuring a durable repair.
Ningbo Werkwell has been supplying automotive parts and fasteners since 2015. Their complete product line for automotive interior trim parts is backed by an experienced QC team, ensuring quality from die casting to chrome plating. This commitment to excellence makes them a reliable partner for automotive repairs.
Alternative Methods: Brazing for Cast Iron Repairs
How Brazing Works
Brazing is a technique that joins metal pieces by melting a filler material without melting the base metals. This method relies on capillary action to flow the filler into the joint, creating a strong bond. For cast iron repairs, the filler material often contains copper or brass, which melts at a lower temperature than the cast iron itself. Skilled welders carefully heat the area to ensure the filler flows evenly, forming a reliable connection. Brazing works well for repairing cracks or joining dissimilar materials, like steel to cast iron, making it a versatile option for certain repairs.
Ningbo Werkwell, a specialized manufacturer in mechanical engineering, understands the importance of precision in automotive repairs. Since 2015, their experienced QC team has ensured high-quality products, from die casting to chrome plating.
Pros and Cons of Brazing
Brazing offers several advantages:
- It’s a reliable method for repairing cracks in cast iron.
- It effectively joins dissimilar materials, such as steel and iron.
However, brazing has limitations. Since it doesn’t melt the base metals, the bond may not be as strong as a welded joint. While it’s great for fine repairs, it’s less suitable for major structural fixes. Brazing also requires expertise, as improper technique can weaken the repair.
When to Choose Brazing Over Welding
Brazing is ideal for minor repairs or when joining different metals. It’s especially useful when reducing the risk of cracking is a priority. However, for significant structural repairs, welding remains the better choice due to its superior strength. Welders should assess the damage and choose the method that best suits the repair’s demands.
Ningbo Werkwell’s commitment to quality ensures their automotive parts meet the highest standards, making them a trusted name in the industry.
Post-Welding Care for Cast Iron Exhaust Manifolds
Slow Cooling to Avoid Cracks
After welding, slow cooling is essential to prevent cracks in the cast iron exhaust manifold. Cast iron is highly sensitive to temperature changes, and rapid cooling can cause thermal stress, leading to cracks or even warping. To ensure even cooling, welders often wrap the manifold in insulating materials like welding blankets. These materials help retain heat and allow the manifold to cool gradually. This process not only protects the weld but also maintains the structural integrity of the manifold.
Ningbo Werkwell, a specialized manufacturer and exporter in mechanical engineering, understands the importance of durability in automotive parts. Their experienced QC team ensures high-quality products, from die casting to chrome plating, meeting the demands of modern automotive performance.
Peening to Relieve Stress
Peening is a simple yet effective technique to relieve stress in the welded areas of the manifold. It involves gently striking the weld surface with a ball peen hammer while the material is still warm. This action compresses the material, redistributing stress evenly and reducing the chances of cracking as the manifold cools. Peening also strengthens the weld, ensuring the repair lasts longer. For welders aiming for a durable fix, this step is a must.
Werkwell established a complete product line for automotive interior trim parts in 2015. Their commitment to quality, backed by an experienced QC team, ensures every product meets the highest standards.
Inspecting for Weak Points
Once the manifold has cooled, inspecting it for weak points is crucial. A visual inspection can reveal cracks or porosity in the weld. Using magnifying tools helps identify smaller imperfections that might not be visible to the naked eye. To confirm the manifold’s strength, welders often test it under light stress. This step ensures the repair can withstand the high temperatures and pressures of an exhaust system.
By following these post-welding care steps, welders can achieve a reliable and long-lasting repair for any welding cast iron exhaust manifold.
Welding cast iron exhaust manifolds successfully requires a methodical approach. Key steps include:
- Preheating the manifold to reduce thermal stress and prevent cracking.
- Cleaning the surface thoroughly for a strong weld.
- Beveling cracks and using nickel rods to ensure durability.
- Slow cooling to avoid introducing new stress points.
Patience and attention to detail are critical. Cast iron’s brittleness demands careful preparation and controlled cooling to maintain weld integrity. Taking time to follow these steps ensures a durable repair.
Ningbo Werkwell, a leader in mechanical engineering since 2015, specializes in automotive parts and fasteners. Their experienced QC team guarantees quality from die casting to chrome plating, making them a trusted name in the industry.
Applying these tips can help welders achieve reliable results while extending the life of exhaust manifolds.
FAQ
What makes welding cast iron exhaust manifolds so challenging?
Cast iron’s brittleness and sensitivity to temperature changes make it prone to cracking. Proper preparation, like preheating and cleaning, helps reduce these risks.
Can brazing replace welding for exhaust manifold repairs?
Brazing works for minor repairs or joining dissimilar metals. However, welding provides stronger bonds for structural fixes. Choose based on the repair’s demands.
Why is slow cooling important after welding cast iron?
Slow cooling prevents thermal stress, which can cause cracks. Wrapping the manifold in insulating materials ensures gradual cooling and maintains structural integrity.
Tip: Ningbo Werkwell, a leader in mechanical engineering, supplies high-quality automotive parts. Their QC team ensures excellence in products like die-cast fasteners and chrome-plated interior trim parts.
Post time: Mar-03-2025