The Duramax engine harmonic balancer maintenance is crucial for optimal engine performance. Neglecting this component can lead to severe issues, as experts emphasize, “Upgrade it early in your engine build process.” To ensure smooth operation, understanding the top 5 maintenance tips is essential. As Xtreme Diesel Performance notes, “Unfortunately, there are no warning signs that you’ll notice without visually inspecting the dowel pin.” The Truck Stop warns of potential risks, stating, “There’s HUNDREDS of broken DURAMAX cranks from guys running aftermarket balancers on engines with virtually no run time.”
Regular Inspection
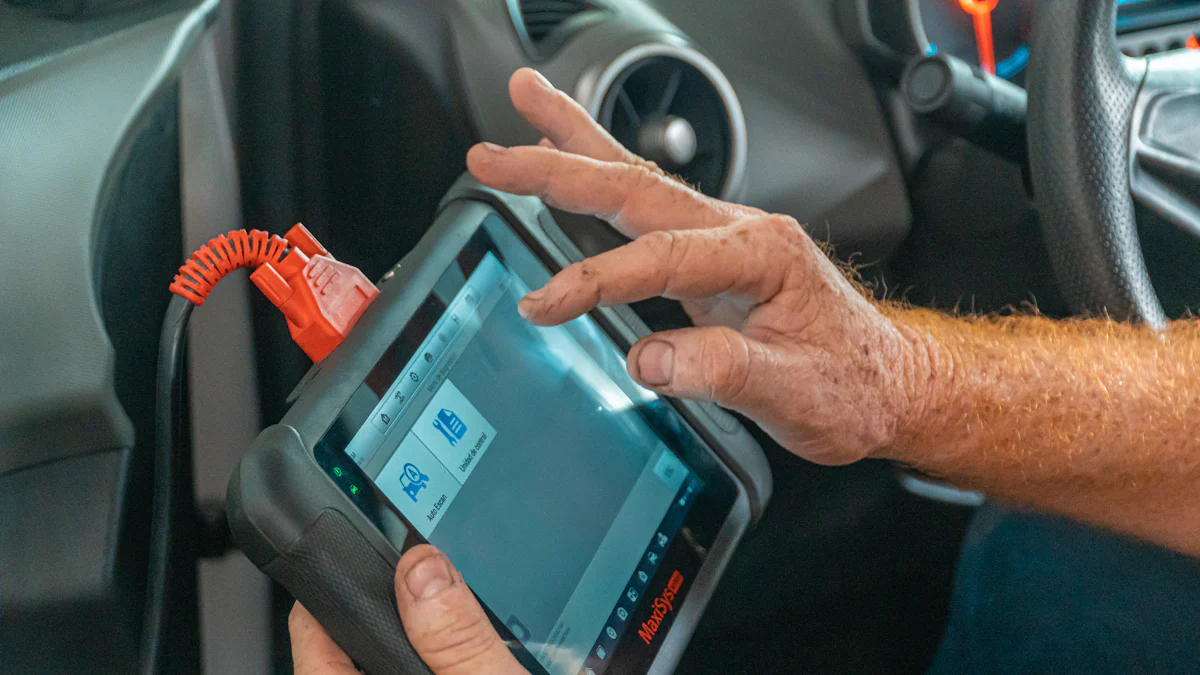
Visual Checks
Signs of Wear
Inspecting the harmonic balancer for signs of wear is crucial in maintaining optimal engine performance. Harmonic Balancer experts highlight that the rubber separating between the two halves of the balancer tends to wear out, especially on the back side. This wear can lead to a noticeable thumping sound, often attributed to the pulley bolts surrounded by rubber. To address this issue effectively, it is recommended to replace both the pulley and balancer simultaneously.
Cracks and Damage
Another essential aspect of visual inspection involves checking for cracks or damage on the harmonic balancer. Cracked, bulging, or missing rubber components can significantly impact the balancer’s functionality. Xtreme Diesel Performance emphasizes the importance of identifying any irregularities in the balancer’s structure promptly. Addressing these issues early on can prevent further damage and ensure smooth engine operation.
Listening for Noise
Unusual Sounds
Listening for unusual sounds can provide valuable insights into the condition of the harmonic balancer. If you notice any unfamiliar noises coming from your engine, it could indicate potential issues with the balancer. Pay close attention to any abnormal sounds during engine operation, as they may signal underlying problems that require immediate attention.
Vibration Indicators
In addition to listening for noise, monitoring vibration indicators is essential for detecting harmonic balancer issues. Vibrations that feel out of place or excessive could be a sign of imbalance within the balancer. Properly functioning harmonic balancers are designed to minimize vibrations and maintain engine stability. Any deviations from normal vibration patterns should be investigated promptly to prevent further complications.
Scheduled Maintenance
Manufacturer Recommendations
Following manufacturer recommendations for scheduled maintenance is key to prolonging the lifespan of your harmonic balancer. Manufacturers provide guidelines on when inspections and potential replacements should occur based on usage and environmental factors. Adhering to these recommendations ensures that your harmonic balancer remains in optimal condition, reducing the risk of unexpected failures.
Frequency of Inspections
Regular inspections play a vital role in ensuring the longevity and efficiency of your harmonic balancer. Setting a consistent schedule for inspections allows you to proactively identify any issues before they escalate into more significant problems. By incorporating frequent checks into your maintenance routine, you can address potential concerns early on and maintain peak performance levels.
By prioritizing visual checks, listening for unusual sounds, and adhering to scheduled maintenance practices, Duramax owners can safeguard their engines against potential harmonic balancer-related issues. Stay proactive in your maintenance efforts to enjoy a smooth driving experience and extend the life of your vehicle’s crucial components.
Proper Tools
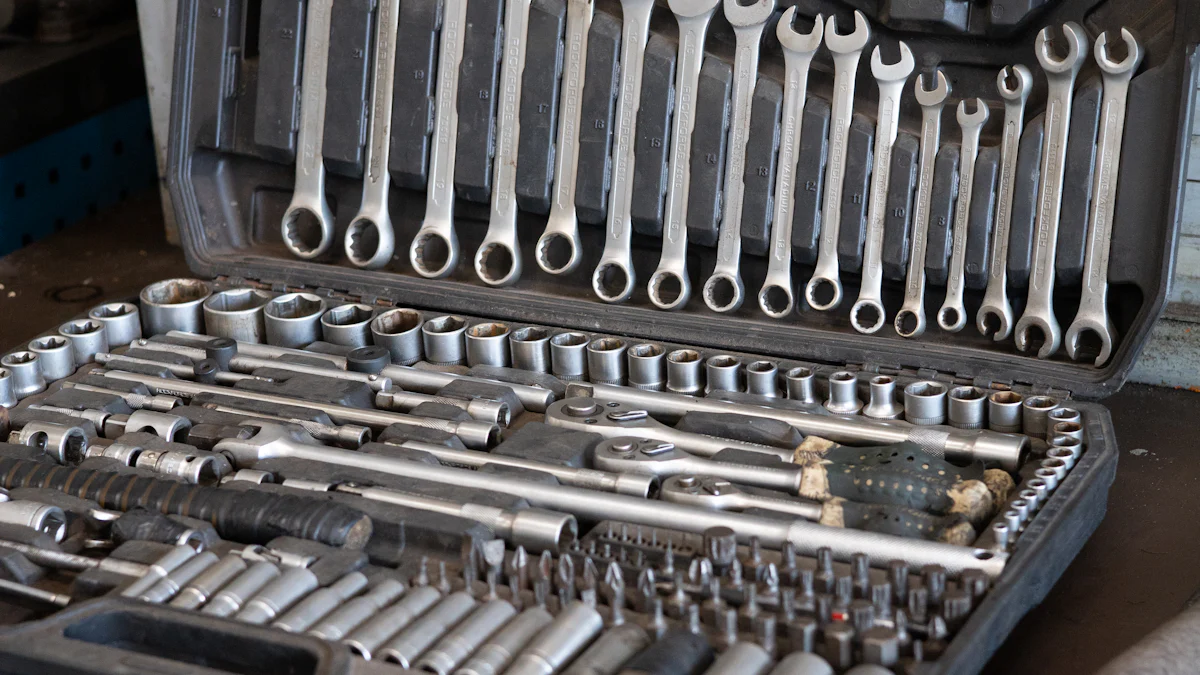
Essential Tools
Harmonic Balancer Puller
To effectively remove the harmonic balancer for maintenance tasks, utilizing a Harmonic Balancer Puller is essential. This tool is specifically designed to safely extract the balancer without causing damage to surrounding components. By securely attaching to the balancer and providing the necessary leverage, the puller simplifies the removal process, making it more efficient and reducing the risk of potential mishaps.
Torque Wrench
When it comes to installing or reassembling the harmonic balancer, a Torque Wrench is a must-have tool in your arsenal. Properly torquing the bolts that secure the balancer is crucial for ensuring its stability and functionality. The torque wrench allows you to tighten the bolts to the manufacturer’s specifications accurately, preventing under or over-tightening that could lead to issues down the line. With precise torque control, you can maintain optimal performance and longevity of your harmonic balancer.
Specialized Tools
Gearwrench Installer
For seamless installation of harmonic balancers, a Gearwrench Installer proves to be invaluable. This specialized tool facilitates the proper alignment and fitting of the balancer onto the crankshaft, ensuring a secure and precise installation. The Gearwrench Installer streamlines the process by providing a reliable method for positioning the balancer correctly without risking misalignment or damage during assembly.
Crankshaft Pin Kits
In situations where replacing pinned harmonic balancers is necessary, Crankshaft Pin Kits offer a convenient solution without requiring extensive machining or removal of the existing balancer. These kits include all the essential components needed to replace pinned balancers efficiently, saving time and effort during maintenance tasks. By utilizing Crankshaft Pin Kits, Duramax engine owners can simplify the replacement process and maintain their engines with ease.
Safety Equipment
Gloves and Goggles
Prioritizing safety during maintenance procedures is paramount, which is why wearing Gloves and Goggles is highly recommended when working on your vehicle’s harmonic balancer. Gloves protect your hands from sharp edges or hot surfaces while handling tools or components, reducing the risk of injuries. Additionally, goggles shield your eyes from debris or fluids that may pose hazards during maintenance activities. By donning appropriate safety gear, you create a safer work environment for yourself while performing essential maintenance tasks on your Duramax engine.
Secure Work Area
Establishing a Secure Work Area before beginning any maintenance work on your harmonic balancer is crucial for both efficiency and safety. Ensure that your workspace is well-lit, organized, and free from clutter to prevent accidents or misplaced tools. Securing loose items and creating a stable work surface minimizes risks associated with working on heavy components like harmonic balancers. By maintaining a secure work area, you can focus on completing tasks effectively while prioritizing safety throughout the maintenance process.
By equipping yourself with essential tools like Harmonic Balancer Pullers and Torque Wrenches, along with specialized equipment such as Gearwrench Installers and Crankshaft Pin Kits, you can streamline maintenance tasks for your Duramax engine’s harmonic balancer. Prioritize safety by wearing Gloves and Goggles while working in a Secure Work Area to ensure smooth operations and prevent potential accidents during maintenance activities.
Installation Tips
Preparation Steps
Cleaning the Area
When preparing to install a Harmonic Balancer, it is essential to start by cleaning the surrounding area meticulously. Any dirt, debris, or residue on the crankshaft or balancer mounting surface can interfere with the proper alignment and installation of the new balancer. Use a clean cloth or a mild solvent to remove any contaminants thoroughly. Ensuring a pristine work environment sets the stage for a successful and secure installation process.
Aligning the Balancer
Proper alignment of the Harmonic Balancer is critical to its functionality and longevity. Before mounting the balancer onto the crankshaft, carefully align the keyway and dowel pin to guarantee a precise fit. Misalignment during installation can lead to increased vibrations, premature wear, and potential damage to both the balancer and engine components. Take your time to align the balancer correctly for optimal performance.
Torque Specifications
Importance of Proper Torque
Understanding and adhering to the manufacturer’s specified torque requirements are paramount when installing a Harmonic Balancer. Improper torque application can have detrimental effects on the balancer’s performance and overall engine operation. Insufficient torque may result in loose components, while excessive torque can lead to structural damage or misalignment issues. Following recommended torque specifications ensures that the balancer functions as intended, reducing the risk of malfunctions or failures.
Step-by-Step Guide
To achieve accurate torque application during Harmonic Balancer installation, consider following a step-by-step guide for optimal results. Begin by hand-tightening the balancer bolt until it makes contact with the crankshaft snout. Utilize a calibrated torque wrench to gradually tighten the bolt in incremental stages according to manufacturer guidelines. Implementing a systematic approach helps distribute torque evenly across all fasteners, promoting stability and balance within the assembly.
Final Checks
Ensuring Proper Fit
After securing the Harmonic Balancer in place, conduct thorough checks to ensure that it is properly fitted onto the crankshaft. Verify that all alignment marks align correctly, indicating that the balancer is seated flush against its mounting surface. Any gaps or misalignments should be addressed promptly before finalizing the installation process. A snug and precise fit guarantees optimal performance and reduces risks associated with improper seating.
Testing The Installation
Once you have completed installing and verifying proper fitment of the Harmonic Balancer, it is crucial to perform comprehensive testing procedures before operating your vehicle. Start by manually rotating the engine by hand to confirm smooth rotation without any obstructions or unusual resistance. Listen for any abnormal noises or vibrations that could indicate installation errors or misalignments. Conducting rigorous testing ensures that your harmonic balancer is securely installed and ready for regular engine operation.
Duramax harmonic balancer maintenance is a critical aspect of engine care, ensuring longevity and performance. Remember the advice from experienced individuals: “Swap a balancer in duramax every 150,000 miles and watch the crank live.” The DURAMAX engine’s unique characteristics can lead to harmonic issues if not addressed proactively. By following the top 5 maintenance tips diligently, owners can prevent potential problems and enjoy a smoother driving experience. Stay ahead of maintenance schedules and prioritize your duramax harmonic balancer for optimal engine health.
Post time: May-31-2024