The verification of torque specifications is paramount in ensuring product quality, safety, and reliability. Neglecting to tighten even a three-cent fastener adequately can result in catastrophic failures. Using torque wrenches diligently prevents bolt failures and assembly issues, as over-torquing can lead to broken studs. Following torque specifications for engine harmonic balancer parts is crucial to prevent fatigue damage and ensure proper sealing. Trusting the specified ls harmonic balancer bolt torque values is key, as they are meticulously determined to maintain optimal performance.
Harmonic Balancer Torque Specs
When it comes to the Harmonic Balancer Torque Specs, precision and accuracy are paramount. The importance of torque specs cannot be overstated, as they ensure the proper functioning and longevity of your engine components. By adhering to the recommended torque values, you can prevent issues such as bolt failure and assembly complications. Let’s delve into the specifics of general torque specs and explore the common values that play a crucial role in maintaining your engine’s health.
General Torque Specs
Importance of Torque Specs
Ensuring that every bolt is tightened to the correct specification is essential for the overall performance and safety of your engine. The torque specs serve as a guideline to prevent under or over-tightening, which could lead to severe consequences. By following these specifications diligently, you guarantee that each component is securely fastened, minimizing the risk of malfunctions.
Common Torque Values
- Valve Lifter Guide Bolts for LS2 require 89 inch lbs., while LS1/LS3/LS6/LS7 need 106 inch lbs.
- Ignition Coil-to-Bracket Bolts should be torqued at 106 inch lbs. for LS1/LS6 and 89 inch lbs. for LS2/LS3/LS7.
- Throttle Body Bolts demand 106 inch lbs. for LS1/LS6 and 89 inch lbs. for LS2/LS3/LS7 engines.
- Oil Pan Closeout Cover Bolt (Left Side) requires 106 inch lbs. for LS1/LS6 and 80 inch lbs. for LS2/LS7.
- Oil Pan Closeout Cover Bolt (Right Side) specifies 106 inch lbs. for LS1/LS6 and 80 inch lbs. for LS2/LS7 engines.
Specific Engine Models
LS1/LS2/LS3 Engines
For specific engine models like LS1, LS2, and LS3, it’s crucial to follow the designated torque specifications meticulously to maintain optimal performance levels. Each engine model has unique requirements that must be met during installation to ensure smooth operation and longevity.
LS7/LS9/LSA Engines
On the other hand, engines such as LS7, LS9, and LSA have their own set of torque values that must be strictly adhered to during assembly processes. These high-performance engines demand precise torque application to guarantee peak efficiency and reliability.
Tools and Materials
Required Tools
- A reliable torque wrench is indispensable when working on harmonic balancers to achieve accurate tightening according to specifications.
- Proper socket sets with various sizes are necessary for accessing different bolts within the engine compartment efficiently.
- Thread lubricants like Loctite are essential for securing bolts effectively while preventing loosening due to vibrations.
Recommended Materials
- High-quality gaskets play a vital role in ensuring proper sealing between components, preventing leaks that could compromise engine performance.
- Clean rags or towels are handy for wiping off any excess lubricants or debris during the installation process.
- Safety goggles protect your eyes from potential hazards like debris or chemicals while working on your engine.
By understanding the significance of harmonic balancer torque specs, you equip yourself with the knowledge needed to maintain your engine’s health effectively through proper installation procedures using appropriate tools and materials.
LS Harmonic Balancer Bolt Torque
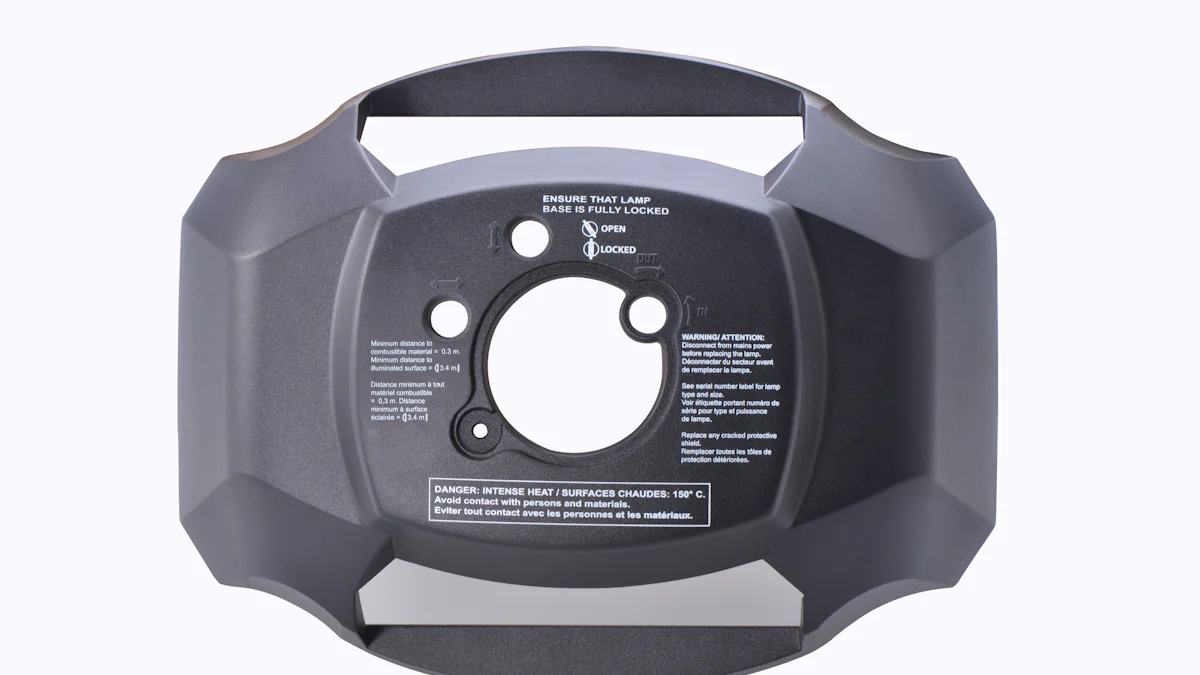
Detailed Torque Specs
When it comes to the LS Harmonic Balancer Bolt Torque, precision is paramount for the proper functioning of your engine. Understanding the detailed torque specifications ensures that each component is securely fastened, minimizing the risk of malfunctions and ensuring optimal performance. Let’s delve into the factory and aftermarket specifications to guide you through this critical process.
Factory Specifications
Chevrolet Performance offers high-quality Harmonic Balancer Bolts made of heat-treated steel for extra strength. These bolts are designed to withstand the rigors of engine operation, featuring a hex head that prevents socket slippage during tightening or loosening. For LS engines like LS1/LS2/LS6, the Crankshaft Balancer Bolt should be torqued to 240 ft-lbs during installation to ensure complete balancer installation.
Aftermarket Specifications
For aftermarket options, consider using Harmonic Balancer Bolts from reputable brands like Werkwell. These bolts are engineered to meet industry standards and provide reliable performance. When following ATI instructions, it is recommended to use Loctite 262 and torque the bolt to 230 ft-lbs for secure installation.
Installation Procedures
Proper installation procedures are crucial for maintaining the integrity of your engine components. By following a step-by-step guide and avoiding common mistakes, you can ensure that the harmonic balancer bolt is securely fastened for optimal performance.
Step-by-Step Guide
- Begin by preparing your workspace with all necessary tools and materials.
- Ensure that the engine is properly supported before starting the installation process.
- Use a reliable torque wrench to tighten the harmonic balancer bolt according to factory or aftermarket specifications.
- Verify that the bolt is torqued to the recommended value using a calibrated torque wrench.
- Double-check all connections and components before proceeding with further engine assembly.
Common Mistakes
- One common mistake during harmonic balancer bolt installation is over-torquing, which can lead to thread damage or component failure.
- Using an incorrect torque value or failing to follow proper installation procedures can compromise the integrity of the engine assembly.
- Neglecting regular inspections or maintenance checks may result in loose bolts or improper alignment, affecting overall engine performance.
Maintenance Tips
Regular maintenance is key to ensuring long-term reliability and performance from your engine components. By conducting routine inspections and addressing any issues promptly, you can prevent potential problems and prolong the lifespan of your vehicle.
Regular Inspections
- Periodically check the tightness of the harmonic balancer bolt to ensure it remains within specified torque values.
- Inspect surrounding components for signs of wear or damage that may affect bolt security.
- Monitor engine vibrations and unusual noises that could indicate loose fasteners or misalignment issues.
Troubleshooting Issues
- If you encounter any difficulties with your harmonic balancer bolt, consult manufacturer guidelines or seek professional assistance.
- Address any abnormal symptoms promptly to prevent further damage or safety hazards associated with loose fasteners.
By adhering to detailed torque specifications, following proper installation procedures, and implementing regular maintenance practices, you can safeguard your engine’s health and optimize its performance for years to come.
Installation Tips
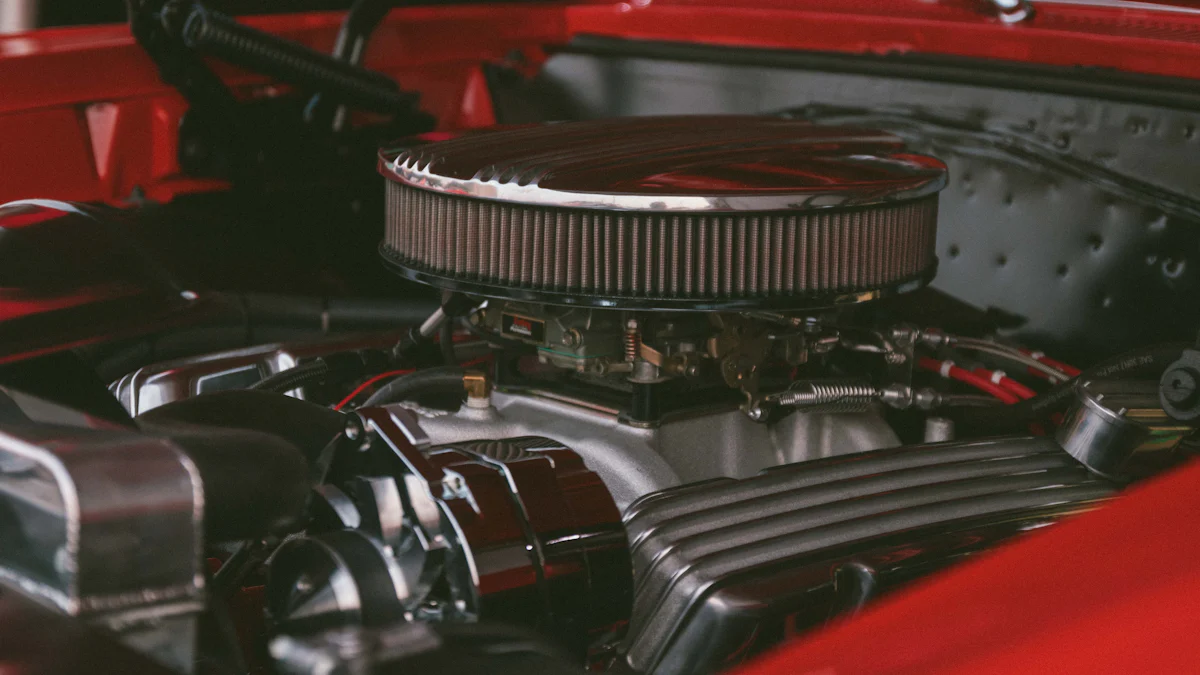
Preparation Steps
When it comes to preparation steps for installing a harmonic balancer bolt, ensuring safety measures is the top priority. Mechanics and car enthusiasts alike understand the importance of creating a secure environment before diving into any engine work. By following these safety guidelines, you can safeguard yourself and others from potential hazards.
Safety Measures
- Prioritize Personal Protective Equipment (PPE) such as safety goggles, gloves, and appropriate clothing to shield yourself from debris or harmful substances.
- Secure the vehicle on a stable surface using jack stands and wheel chocks to prevent any accidental movement during the installation process.
- Disconnect the battery to avoid electrical mishaps while working on engine components.
- Keep your workspace well-ventilated to dissipate fumes or exhaust gases that may accumulate during engine operation.
Workspace Setup
Setting up your workspace efficiently is essential for a smooth installation process. Organizing your tools and materials in advance can save time and prevent unnecessary delays. Here are some tips for optimizing your workspace setup:
- Arrange your tools in an orderly manner within reach to avoid searching for them mid-task.
- Use a clean and well-lit area to enhance visibility while working on intricate engine components.
- Lay down protective mats or covers to shield sensitive parts of the vehicle from accidental damage or scratches.
- Have a fire extinguisher nearby as a precautionary measure in case of emergencies.
Installation Techniques
Proper alignment and precise torque application are critical aspects of installing a harmonic balancer bolt correctly. Understanding the intricacies of these techniques ensures that your engine operates smoothly without any issues arising from improper installation methods.
Proper Alignment
Achieving proper alignment when installing the harmonic balancer bolt is crucial for maintaining the balance and integrity of the engine components. Misalignment can lead to excessive vibrations, premature wear, or even catastrophic failures down the line. Follow these alignment guidelines for a successful installation:
- Align the keyway on the crankshaft with the corresponding slot on the harmonic balancer before securing it in place.
- Use alignment tools or marks provided by manufacturers to ensure accurate positioning during installation.
- Double-check alignment multiple times throughout the process to guarantee precision before finalizing torque application.
Torque Application
Applying torque correctly is paramount when fastening the harmonic balancer bolt to specified values. Over-tightening can cause thread damage or component failure, while under-tightening may result in loose connections that compromise engine performance.
- Utilize a calibrated torque wrench set at the recommended value provided by manufacturer specifications for precise tightening.
- Apply torque gradually in incremental stages rather than all at once to distribute pressure evenly across threads and prevent sudden shifts in tension.
- Verify torque values using reliable gauges after initial application to confirm proper fastening before proceeding with additional assembly tasks.
Post-Installation Checks
After completing the installation process, conducting thorough post-installation checks ensures that everything is securely fastened and functioning as intended. Verifying torque values and performing test runs are essential steps towards confirming successful installation outcomes.
Verifying Torque
Once you’ve tightened the harmonic balancer bolt according to specifications, it’s vital to verify that each fastener meets prescribed torque values accurately.
- Revisit each connection point with a calibrated torque wrench to confirm that all bolts are torqued correctly without deviations.
- Check for any signs of loosening or irregularities that may indicate inadequate tightening during initial installation procedures.
Test Runs
Conducting test runs after verifying torque values provides real-world validation of your installation efforts. These test runs allow you to observe how well your engine performs under operational conditions post-installation.
- Start with short test runs at varying speeds to assess overall engine performance and identify any unusual vibrations or noises.
- Monitor temperature levels, fluid leaks, and other indicators that could signal potential issues related to improper harmonic balancer bolt installation.
By adhering strictly to preparation steps, implementing proper alignment techniques, applying precise torque application methods, verifying torques post-installation, and conducting thorough test runs, you ensure optimal performance from your engine components secured by harmonic balancer bolts.
Testimonials:
- Certified A&P:
“Torque specs are basically gospel in my world.”
- Engineer:
“I’m an engineer that sometimes comes up with torque specs for engine parts.”
- Unknown:
“Trust the torque values. They know what works better than you.”
By recapitulating the key points and emphasizing the significance of adhering to specified torque values, individuals ensure optimal engine performance. Following torque specifications diligently is essential to prevent potential failures and maintain the integrity of engine components. Remember, precision in torque application is paramount for sustaining engine health and longevity. Trust the expertise behind the provided torque values; they are meticulously determined for your engine’s well-being.
Post time: Jun-04-2024