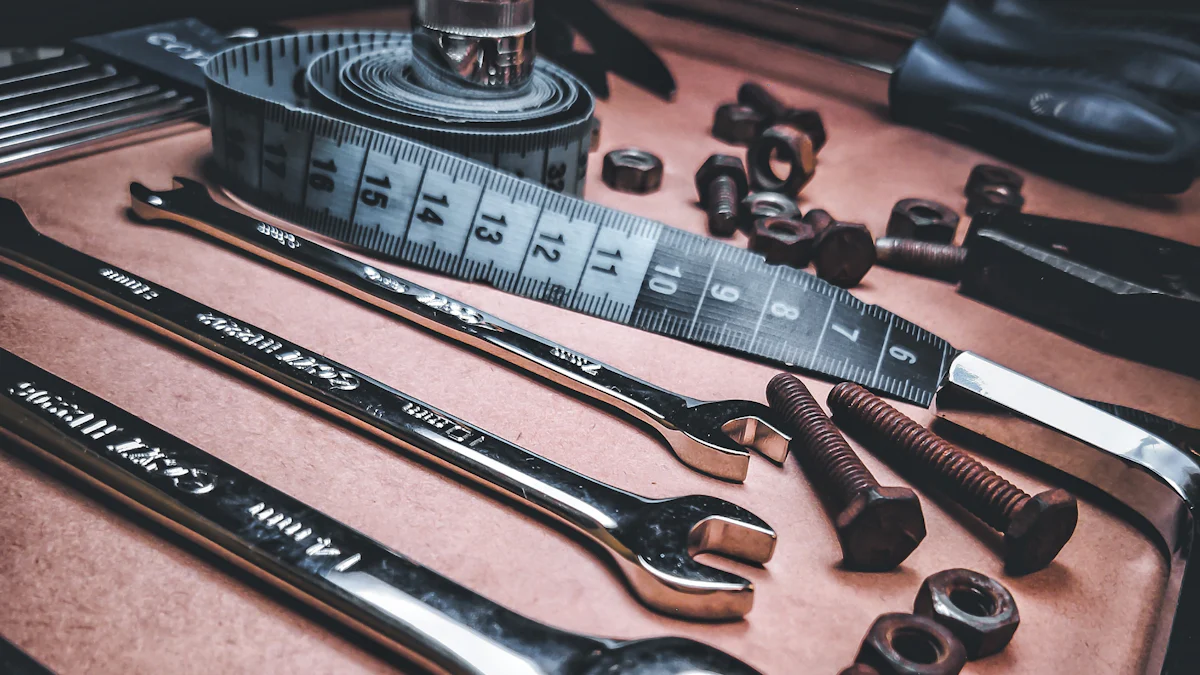
Understanding the 5.3 harmonic balancer bolt socket size is paramount for any mechanic working on a 5.3 engine. The harmonic balancer plays a crucial role in engine performance, making it essential to grasp its intricacies. With the TECH Fanatic Thread Starter as a valuable resource, enthusiasts can delve deeper into this topic and enhance their knowledge base.
Understanding the 5.3 Harmonic Balancer Bolt
When considering the harmonic balancer bolt of a 5.3 engine, one must delve into its intricate details to comprehend its significance fully. The balancer bolt is not merely a fastener; it serves as a vital component that ensures the harmonious operation of the engine. By exploring the specifics of the harmonic balancer bolt, individuals can gain a profound insight into its role within the engine system.
Specifications of the Bolt
Size and Threading
The harmonic balancer bolt size for a 5.3 engine is M16 x 2.0, indicating its precise dimensions and threading specifications. This particular size ensures a secure fit and proper alignment, crucial for maintaining optimal engine performance. The threading of the balancer bolt is designed to withstand significant forces and vibrations, underscoring its durability and reliability.
Material and Durability
Crafted from high-quality materials, the harmonic balancer bolt exhibits exceptional durability and strength characteristics essential for withstanding the rigors of engine operation. Its robust construction guarantees long-term functionality, contributing to the overall stability and efficiency of the engine system.
Role in Engine Performance
Importance of Proper Installation
The correct installation of the harmonic balancer bolt is paramount for ensuring seamless engine performance. A meticulously executed installation process guarantees that the harmonic balancer remains securely attached to the crankshaft, preventing any potential disruptions in engine function. Proper installation procedures are fundamental in maximizing the longevity and effectiveness of this critical component.
Potential Issues with Incorrect Size
Using an incorrect socket size when handling the harmonic balancer bolt can lead to detrimental consequences for the engine system. An ill-fitting socket may compromise the integrity of the fastening mechanism, posing a risk of loosening or detachment during operation. Such issues underscore the importance of utilizing precise tools and techniques when working with essential components like the harmonic balancer bolt.
TECH Fanatic Thread Starter Insights
Community Discussions
Within forums like TECH Fanatic Thread Starter, enthusiasts engage in vibrant discussions regarding various aspects of automotive maintenance, including insights on balancer bolts. These community interactions provide valuable perspectives on best practices, troubleshooting techniques, and innovative approaches to addressing common challenges related to harmonic balancers.
Expert Opinions
Experts within platforms like TECH Fanatic Thread Starter offer invaluable insights into optimizing balancer bolt performance and longevity. Their wealth of experience and knowledge enables them to provide practical advice on maintenance strategies, torque specifications, and diagnostic methods tailored to enhance overall engine efficiency.
Tools Required for the Job
Socket Sizes
1 1/8 inch Socket
When it comes to tackling the 5.3 harmonic balancer bolt, having the right tools at your disposal is non-negotiable. The 1 1/8 inch socket emerges as a key player in this scenario, offering a precise fit for the bolt’s dimensions. Its compatibility with the M16 x 2.0 threading ensures a secure grip, essential for seamless installation and removal processes.
1 5/16 inch Socket
For those instances where a more robust approach is required, the 1 5/16 inch socket steps in to handle the task with finesse. This larger socket size caters to the specific needs of the harmonic balancer bolt, providing a snug fit that facilitates efficient removal procedures. Its versatility and durability make it an indispensable tool in your automotive arsenal.
Additional Tools
Impact Gun
In the realm of automotive maintenance, precision and efficiency are paramount. An impact gun serves as a reliable companion when dealing with components like the harmonic balancer bolt. Its high-torque output streamlines the removal process, saving valuable time and effort. With the right impact gun by your side, tasks that once seemed daunting become more manageable.
Torque Wrench
Ensuring that the harmonic balancer bolt is tightened to exact specifications is crucial for optimal engine performance. A torque wrench offers precision control over tightening levels, preventing under or over-torquing scenarios that could compromise component integrity. By incorporating a torque wrench into your toolkit, you elevate your maintenance practices to a professional standard.
Safety Equipment
Gloves and Eye Protection
Prioritizing safety during any automotive endeavor is non-negotiable. Equipping yourself with gloves and eye protection shields you from potential hazards, ensuring a secure working environment. These safety essentials not only safeguard your well-being but also enhance your focus and confidence as you navigate intricate tasks like handling the harmonic balancer bolt.
Proper Work Environment
Creating an optimal work environment sets the stage for successful maintenance operations. Establishing a workspace that is clean, well-lit, and organized fosters efficiency and reduces risks of errors or accidents. By adhering to best practices for workspace organization, you cultivate a professional approach to handling tasks involving critical components like the harmonic balancer bolt.
By embracing these essential tools and safety measures, you equip yourself with the knowledge and resources needed to navigate the intricacies of working with the 5.3 harmonic balancer bolt effectively. Remember, precision and diligence are key when engaging with vital engine components—empower yourself with the right tools for the job!
Practical Tips for Handling the Bolt
Removal Process
When approaching the harmonic balancer bolt removal process, precision and caution are paramount. To initiate the removal procedure effectively, begin by ensuring that all necessary tools are readily available. This includes the 1 5/16 inch socket or a 34mm socket, specifically designed to accommodate the dimensions of the bolt. By selecting the appropriate socket size, mechanics can establish a secure connection with the bolt, facilitating a seamless removal experience.
Once equipped with the requisite tools, proceed to position the socket securely onto the harmonic balancer bolt. Apply consistent pressure in a clockwise direction to loosen the bolt gradually. Avoid abrupt movements or excessive force, as these actions may result in damage to both the bolt and surrounding components. By adopting a methodical approach and exercising patience throughout this process, individuals can effectively disengage the harmonic balancer bolt without encountering unnecessary complications.
Step-by-Step Guide
- Gather all necessary tools for harmonic balancer bolt removal.
- Select an appropriate socket size based on specifications (e.g., 1 5/16 inch or 34mm).
- Position the socket securely onto the bolt and apply clockwise pressure.
- Loosen the bolt gradually to disengage it from its fastening mechanism.
- Exercise caution and avoid applying excessive force during removal.
Common Challenges
- Over-tightened Bolts: In some instances, mechanics may encounter harmonic balancer bolts that have been excessively tightened, posing challenges during removal. To address this issue, consider utilizing penetrating oil to lubricate and loosen stubborn bolts gradually.
- Corrosion Build-Up: Bolts exposed to environmental elements may develop corrosion over time, hindering their removal process. Implement rust-penetrating solutions or heat induction techniques to break down corrosion and facilitate smoother extraction procedures.
Installation Process
Assembling a harmonic balancer bolt demands meticulous attention to detail and adherence to specific guidelines for optimal performance outcomes. Prioritize securing all essential tools before commencing installation activities, including a 1 1/8 inch socket tailored to fit the precise dimensions of the bolt accurately.
Initiate the installation process by aligning the harmonic balancer with its designated position on the crankshaft carefully. Ensure that each component is positioned correctly before introducing the harmonic balancer bolt into its fastening mechanism. Utilize manual torque application methods instead of impact wrenches to prevent potential damage or misalignment issues during installation.
Step-by-Step Guide
- Prepare all necessary tools for installing a harmonic balancer.
- Align the harmonic balancer with its designated location on the crankshaft.
- Insert and tighten the harmonic balancer bolt manually using a torque wrench.
- Verify proper alignment of components post-installation for optimal functionality.
Ensuring Proper Torque
Maintaining accurate torque levels when securing a harmonic balancer bolt is critical for preserving engine integrity and performance efficiency over time. Refer to manufacturer specifications or expert recommendations regarding torque settings suitable for your specific engine model.
To ensure proper torque application, employ a reliable torque wrench calibrated to deliver precise tightening measurements consistently. Avoid utilizing impact guns for this task, as they may lead to overtightening or uneven distribution of torque along critical engine components.
Maintenance Tips
Regular inspections serve as proactive measures in identifying potential issues with your engine’s harmonic balancer system promptly. Schedule routine maintenance checks at specified intervals to assess wear patterns and detect any signs of deterioration affecting component functionality.
During inspections, pay close attention to visible indicators such as unusual noises emanating from the engine bay or irregular vibrations while driving—these symptoms may signify underlying problems with your harmonic balancer assembly requiring immediate attention.
Regular Inspections
- Conduct periodic visual inspections of your engine’s harmonic balancer system.
- Monitor for abnormal sounds or vibrations indicative of potential issues.
- Address any visible wear patterns promptly through professional maintenance services if necessary.
Signs of Wear and Tear
- Listen for unusual noises originating from your engine compartment during operation.
- Watch out for vibrations or rattling sensations while driving that could signal imbalance issues.
- Inspect physical components for signs of wear such as cracks or misalignments impacting overall performance reliability.
By integrating these practical tips into your maintenance routines, you equip yourself with essential knowledge and strategies for handling Engine components like harmonic balancer bolts effectively across various automotive applications.
In the realm of engine maintenance, precision is paramount. Ensuring the correct socket size for the harmonic balancer bolt guarantees seamless operations. Remember to adhere to best practices and consult reputable resources like the TECH Fanatic Thread Starter for expert insights. By summarizing key points and emphasizing the significance of precise tools, mechanics can elevate their craft and optimize engine performance effectively.
Post time: May-28-2024